Contents
AGVs and AMRs: An Overview
The Future of AGVs and AMRs
AGVs vs AMRs: Key Takeaways
Encord Blog
AGV vs. AMRs for Warehouse Automation: What's the Key Difference?
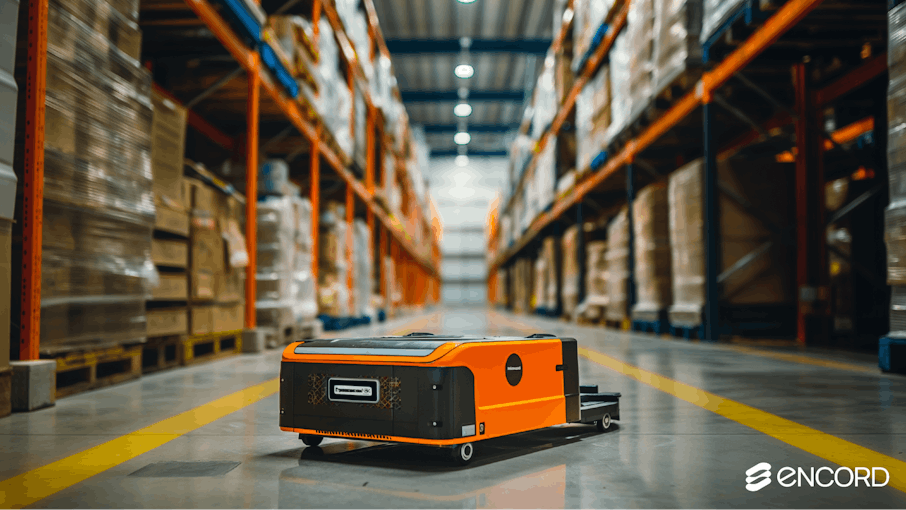
With automation taking center stage in the manufacturing domain to drive profits, businesses are rushing to build the best automated systems for warehouse operations. The high demand is causing the warehouse automation market to boom, with a predicted compound annual growth rate of 13.6% between 2023 and 2024.
Automated guided vehicles (AGVs) and autonomous mobile robots (AMRs) are the most significant tools for automating warehouse functions. While AGVs are more common, AMRs are becoming more popular due to their intelligent navigation capabilities. AMR's commercial success is evident from the staggering revenue of $3.6 billion the AMR market generated in 2022 alone.
This article will discuss AMRs and AGVs and their key differences to help you choose the right system for your needs.
AGVs and AMRs: An Overview
AGVs are self-guided material handling systems for carrying loads in warehouses, distribution centers, and manufacturing plants. They follow fixed paths to move from one place to another, which makes them helpful in structured environments where paths are predictable.
There are multiple AGV types:
- Automated Guided Carts (AGCs): AGCs are the most basic AGV type for transporting small parts. They help transport medical equipment to healthcare facilities without human intervention.
- Forklift AGVs: Automated forklifts for lifting and carrying heavy loads.
- Towing AGVs: Used for pulling other non-autonomous vehicles.
- Unit Load Handlers: Designed to carry items like pallets or totes.
- Heavy Burden Carriers: Used for transporting the heaviest loads, such as coils, plates, and assembly line components.
AMRs are more sophisticated systems that use advanced algorithms for flexible navigation. They are helpful in dynamic environments where adaptability and agility are necessary.
The robots use sensors and computer vision (CV) algorithms to detect obstacles and calculate the most optimal path from the source to the destination.
Evolution of AGVs and AMRs
Barrett Electronics of Northbrook, Illinois, USA, introduced the first AGV in 1953. These vehicles used optical sensors or magnetic fields embedded in the factory floor for navigation.
In the 1960s, the food industry started using AGVs with magnetic and electrical sensors to follow pre-determined paths. Later, in the 1970s, Volkswagen, Germany, introduced AGVs with onboard computers and control cabinets.
It was not until the 1980s that car manufacturers started using AGVs with laser and infrared navigation systems. The first AMR also emerged during the 1980s, which could move in obstacle-free regions using sonar sensors.
In the 1990s, AGVs started using omnidirectional wheels and ultrasonic sensors. A more advanced French AMR, with laser telemetry for better motion planning, also appeared.
Researchers finally introduced AGVs with artificial intelligence (AI) and the first AMR with a robotic arm in the 2000s. Ten years later, in the 2010s, they integrated open-source software and robotic operating systems in AGVs and AMRs.
Today, AGVs and AMRs move in any direction and maneuver through any path while avoiding obstacles. Moreover, Thierry Delmas - Managing Director at Kivnon - notes,
“The tasks and processes that benefit from automation with AGVs/AMRs are continuously expanding. From indoor applications where space is tight to more and more outdoor applications, technological advancements are enabling more possibilities than ever.”
Similarly, modern AGVs, AMRs, and advanced technology are applicable in multiple industries. Jeff Chu - Director at Eckhart - adds,
“We see AGVs deployed in diverse industries, including electric vehicles, aerospace, renewable energy, defense, automotive, and heavy industrial.”
Key Differences
While AGVs and AMRs optimize transportation workflows, they still have a few main differences. The following sections briefly discuss the factors differentiating the two systems to help you choose the right vehicle for your use case.
Navigation
Although AGVs and AMRs can help transport goods and improve warehousing operations, their navigation methods differ.
Navigation includes sensing and localization, path planning, obstacle avoidance, and payload docking.
Sensing and Localization
AGVs use the following methods to estimate their location and sense objects around them.
- Wired: AGVs move through a wired path or follow magnetic strips embedded in the factory floor. The wires or strips emit signals that AGVs detect to navigate around objects.
- Tape: A magnetic tape installed on the factory floor guides AGVs with magnetic sensors.
- Laser Target: AGVs with laser transmitters and receivers emit laser beams. Tapes mounted on walls reflect these beams, and AGVs use them to calculate their current location.
- Inertial Navigation: The system guides AGVs using gyroscopes and accelerometers.
In contrast, AMRs use multi-sensor fusion techniques, which involve gathering image data from cameras, laser and light detection, and ranging (LiDAR) sensors.
AMRs use the data to understand their surroundings and compute their current location.
Path Planning
As discussed above, AGVs follow fixed routes determined through magnetic tapes, wires, and reflectors.
AMRs use CV algorithms to process image data and identify landmarks and image patterns. This information helps robots recognize objects and compute the most optimal path to the destination in real-time.
Obstacle Avoidance
AMRs recognize obstacles by extracting invariant features from images captured through cameras and other sensors. They adjust their paths dynamically by computing alternative routes to avoid collisions.
AGVs, however, have a traffic control system that can include any of the following methods:
- Zone Control: The method uses wireless transmitters that send signals to AGV sensors. The signals inform AGVs whether a particular path is clear. The transmitter sends a “clear” signal indicating the AGV to move or a “stop” signal if other AGVs pass by.
- Collision Avoidance: Sonic or infrared sensors in AGVs emit signals and await a response to determine nearby obstacles.
- Combination Control: AGVs with a combination control system use zone control and collision avoidance sensors for more robust traffic control.
Payload Docking
AMRs automatically detect the correct payload to move and use robotic arms to unload and load items at relevant docking stations.
However, AGVs dock at pre-defined locations and may require manual effort to adjust the payload position to avoid disruptions.
Safety
AMRs have advanced safety features that allow them to detect objects and people and move around them efficiently. They navigate safely in changing environments where multiple obstacles of different types exist.
Conversely, AGVs cannot travel in populated areas as they cannot navigate unstructured environments.
They also need more travel space and a clean environment to ensure their sensors do not malfunction due to dust.
Installation and Deployment
Deploying AMRs is relatively easier than installing AGVs, as AMRs use intelligent algorithms to navigate and perform tasks.
Installing an AGV, however, is more time-consuming as it requires significant infrastructure changes. For instance, users must find adequate space on the factory floor to install wires, tapes, and sensors for AGV navigation.
The path must also be free from large obstacles, and loading and unloading points must have fixed route networks.
Flexibility and Adaptability
Again, AMRs have the upper hand when it comes to flexibility and adaptability. Since AMRs use feature-based localization and path planning, they can handle unexpected situations more efficiently and perform tasks without manual intervention.
Furthermore, AMRs offer more agility in warehouses, as they can move materials more precisely across the factory floor using robotic arms.
AGVs, in contrast, are much less adaptable due to their limited ability to follow pre-defined paths. The user must also reprogram the AGV with new instructions if routes change or new obstacles emerge, causing downtime and operational inefficiency.
Cost
Users must consider the upfront and ongoing investments required to operate AMRs or AGVs to determine the most cost-effective solution.
Usually, AMRs are cheaper to deploy as they require minimal infrastructure changes. However, their initial investment can be significant as they comprise advanced sensors, software, and hardware components. Nevertheless, AMRs have lower operational costs as they require minimal changes to existing infrastructure.
On the contrary, AGVs have higher deployment costs as users must align their existing infrastructure to make it compatible with the AGV’s navigation system.
AGVs can also have more significant maintenance costs associated with maintaining the wires, tapes, and sensors that control their navigation.
Applications
Traditionally, AGVs were more suitable for use cases involving heavy-load transportation, while AMRs carried lighter materials. Today, the boundary between their applications is blurry, and both help streamline material flow in multiple domains.
However, a few differences exist. For instance, AMRs are more versatile and have applications in agriculture, manufacturing, and healthcare, where they are responsible for picking, sorting, and delivering goods to people or distribution centers.
In contrast, manufacturers use AGVs to perform more repetitive tasks, such as supplying heavy items to production lines or conveyor systems.
Overall, AMRs have applications in dynamic settings where tasks require intelligent judgment, whereas AGVs are more helpful in performing routine tasks.
The Future of AGVs and AMRs
Automation is critical to surviving in the modern digital space, where businesses rely heavily on automated systems to reduce operational costs.
AGVs and AMRs are the cornerstones of the current digital revolution. They augment human capabilities by allowing workers to focus more on productive tasks, while these vehicles and robots perform more monotonous duties.
Below are a few potential advancements, challenges, and opportunities that will likely shape the future of AGVs and AMRs.
Potential Advancements
The list below mentions a few advancements that will likely occur in the near future:
Advanced Sensors
While monocular and stereo cameras are the most common devices used for AGV and AMR localization, bionic cameras, LiDAR, and ultrasonic sensors will likely redefine how autonomous vehicles navigate.
Internet-of-Things (IoT)
With IoT driving the industry 4.0 revolution, AGVs and AMRs integrated with IoT devices will soon become the norm, where they collect and analyze extensive data to optimize maneuverability.
Swarm Robots
As research in swarm intelligence continues, robotic solutions will involve a fleet of robots performing together to complete tasks requiring coordination and collaboration.
Challenges
The following is a list of possible challenges users may face when implementing an autonomous system involving AMRs and AGVs.
- Replacing Legacy Systems: Companies may need to replace their existing systems to ensure compatibility with modern AGVs and AMRs. The change may demand significant initial investments and commitments from higher management.
- Data Privacy: As AMRs and AGVs use AI and ML to navigate, reliance on extensive data exposes businesses using these vehicles to privacy risks. Companies must choose vendors with strict data privacy frameworks and guidelines to avoid costly breaches.
- Job Displacement: While individual organizations may save on labor costs due to increased automation, the economy may suffer from increased unemployment as machines replace human workers. Economy-wide implementation of AGVs and AMRs will require careful government policies to manage displaced workers.
Opportunities
Although automation comes with significant challenges, it also offers greater opportunities, as listed below.
- New Business Models: Data privacy concerns and job displacement issues can lead to new business models that efficiently address these challenges. For instance, businesses can introduce training programs and better security protocols to improve data privacy and workforce retention.
- Collaborative Robots: Advancements in AI can result in shared workspaces where humans and robots work collaboratively to solve complex issues in multiple domains, such as healthcare, agriculture, and hospitality.
- Green Technology: As businesses become more environmentally conscious, energy-efficient technology initiatives can allow AMRs and AGVs to use more environmentally friendly batteries and components to reduce their carbon footprint.
AGVs vs AMRs: Key Takeaways
Automated Guided Vehicles (AGVs) and Autonomous Mobile Robots (AMRs) are defining the new wave of automation in multiple industries. Below are a few points to remember regarding these revolutionary systems.
- Differences between AGVs and AMRs: AGVs are autonomous vehicles carrying heavier loads that follow fixed paths. AMRs are intelligent robots that adjust their paths dynamically and carry relatively lighter loads.
- AGV vs. AMR Cost of Ownership: AGVs are more expensive to deploy and maintain as they require significant infrastructure changes. AMRs have lower operational costs but may demand a higher initial outlay.
- AGV and AMR Challenges: Implementing AGVs and AMRs presents several significant challenges, including the cost of replacing legacy systems, data privacy, and job displacement.
Explore our products
- Automated Guided Vehicles (AGVs) are self-guided systems that carry heavy warehouse loads.
- Autonomous Mobile Robots (AMRs) are advanced robotic systems that use sophisticated computer vision algorithms to navigate.
- Automated Guided Carts (AGCs), Towing AGVs, Forklift AGVs, Unit Load Handlers, and Heavy Burden Carriers are a few AGV types.
- AGVs follow a fixed path determined through wires, magnetic tapes, or strips installed on the factory floor.
- AMRs collect image data using cameras, lasers, and ultrasonic sensors and use AI algorithms to navigate and detect obstacles.