Contents
What is a Digital Twin?
Types of Digital Twins
Levels of Digital Twins
Do Digital Twins Use AI?
Digital Twins Examples
How Encord Enhances Digital Twin Models
Key Takeaways
Encord Blog
What is a Digital Twin? Definition, Types & Examples
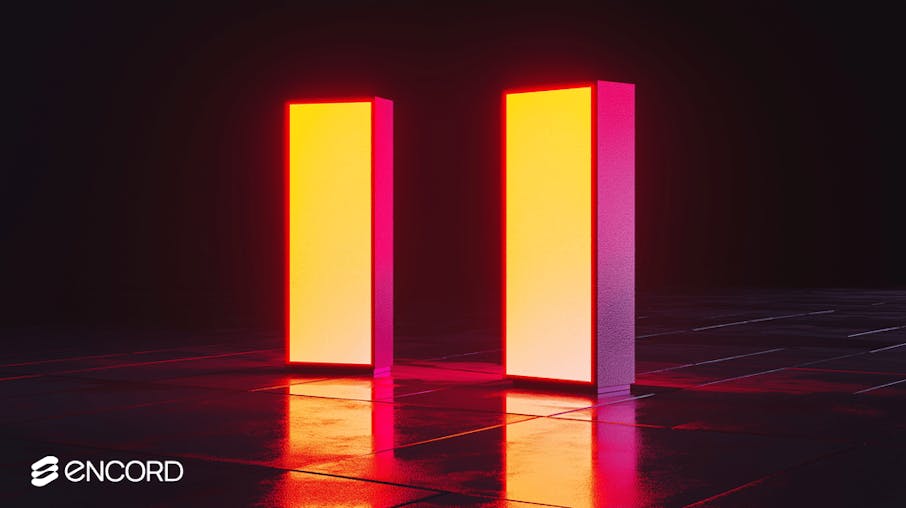
Imagine a busy factory, where all the machines are running and sensors are tracking every detail of how they run. The key technology of this factory is a digital twin, a virtual copy of the whole factory.
Meet Alex, the plant manager, who starts his day by checking the digital twin of the factory on his tablet. In this virtual model, every conveyor belt, robotic arm, and assembly station is shown in real time. This digital replica is not just a static image. It is a dynamic, live model that replicates exactly what is happening within the factory.
Earlier in the week, a small vibration anomaly was detected on one of the robotic arms. In the digital twin, Alex saw the warning signals and quickly zoomed in on the problem area. By comparing the current data with historical trends stored in the model, the system predicted that the robotic arm might experience a minor malfunction in the next few days if not serviced.
Alex then called a meeting with the maintenance team using the insights from the digital twin. The team planned a repair to ensure minimal disruption to production. The digital twin not only helped predict the issue but also allowed the team to simulate different repair scenarios and choose the most efficient one without stopping the production line.
As production increases, the digital twin continues to act as a silent guardian monitoring energy use, optimizing machine settings, and suggesting improvements to reduce waste. It is like having a virtual copy of the factory in the cloud that constantly learns and adapts to make the physical world more efficient.
Digital Twin in Factory (Source)
What is a Digital Twin?
A Digital Twin is a virtual representation of a physical object, system, or process that reflects its real-world version in real-time or near-real-time. It uses data from sensors, IoT devices, or other sources to simulate, monitor, and analyze the behavior, performance, or condition of the physical entity. This concept is widely used in industries like manufacturing, healthcare, urban planning, and more to help improve decision-making, predictive maintenance, and optimization.
Digital twin fundamental technologies (Source)
A Digital Twin is a dynamic, digital copy that grows and changes along with its physical counterpart. It combines data (whether from the past, in real-time, or predictive) with advanced technologies like AI, machine learning, and simulation tools. This allows it to provide insights, predict outcomes, or test scenarios without the need to directly interact with the physical object or system.
A Digital Twin arrangement in automotive industry (Source)
Types of Digital Twins
Digital twins can be categorized into different types based on the scope, complexity of what they represent and application it can perform. Here are four primary types.
Component Twins
Component twins are digital replicas of individual parts or components of a larger system. They focus on the specific characteristics and performance metrics of a single element.
For example, imagine a jet engine where each turbine blade is modeled as a component twin. By tracking stress, temperature, and wear in real time, engineers can predict when a blade might fail and schedule maintenance before a critical issue occurs.
Asset Twins
Asset twins represent entire machines or physical assets. They integrate data from multiple components to provide a collective view of an asset's performance, condition, and operational history.
Consider an industrial robot on a production line. Its digital twin includes data from all its moving parts, sensors, and control systems. This asset twin helps the maintenance team monitor the robot’s overall health, optimize its performance, and schedule repairs to avoid downtime.
System Twins
System twins extend beyond individual assets to represent a collection of machines or subsystems that interact with one another. They are used to analyze complex interactions and optimize performance at a broader scale.
In a smart factory, a system twin might represent the entire production line. It integrates data from various machines, such as conveyors, robots, and quality control systems. This comprehensive model enables managers to optimize workflow, balance loads, and reduce bottlenecks throughout the entire manufacturing process.
Process Twins
Process twins model entire workflows or operational processes. They capture not just physical assets but also the sequence of operations, decision points, and external variables affecting the process.
A supply chain process twin could represent the journey of a product from raw material sourcing to final delivery. By simulating logistics, inventory levels, and transportation routes, businesses can identify potential disruptions, optimize delivery schedules, and enhance overall supply chain efficiency.
Levels of Digital Twins
Digital twins evolve over time as they incorporate more data, analysis, and autonomous capabilities. Here are the 5 Levels of Digital Twins.
Descriptive Digital Twin
A descriptive digital twin is a basic digital replica that mirrors the current state of a physical asset. It represents real-time data and static properties without much analysis. The example of a descriptive digital twin is a digital model of a hospital MRI machine that displays its operating status, temperature, and usage statistics. It shows the current condition but does not analyze trends or predict future issues.
Diagnostic Digital Twin
This level enhances the descriptive twin by adding diagnostic capabilities. It analyzes data to identify deviations, errors, or early signs of malfunction. For example, consider the same MRI machine that now includes sensors and analytics that detect if its cooling system is underperforming. Alerts are generated when operating parameters deviate from normal ranges to enable identification of the issue early.
Predictive Digital Twin
At this stage, the digital twin uses historical and real-time data to forecast future conditions. Predictive analytics help anticipate failures or performance drops before they occur. For a surgical robot, the predictive digital twin analyzes past performance data to predict when a component might fail. This allows maintenance to be scheduled proactively which reduces the risk of unexpected downtime during critical operations.
Prescriptive Digital Twin
It is a more advanced twin that goes beyond prediction to recommend specific actions or solutions, often with “what-if” scenario testing. It combines predictive insights with recommendations or automated adjustments. A digital twin of a hospital’s intensive care unit (ICU) monitors various devices and patient parameters. If the twin predicts a rise in patient load, it might suggest reallocating resources or adjusting ventilator settings to optimize care which ensures the unit runs smoothly during peak times.
Autonomous Digital Twin
It is the most advanced level of digital twins. An autonomous digital twin not only predicts and prescribes actions but can execute them automatically in real time. It uses AI and machine learning to adapt continuously without human intervention. For example, in a fully automated pharmacy system this digital twin monitors medication dispensing, inventory levels, and patient prescriptions. When it detects discrepancies or low stock, it autonomously reorders supplies and adjusts dispensing algorithms to ensure optimal service without waiting for manual input.
Do Digital Twins Use AI?
Digital twins often integrate AI to transform raw data into actionable insights, optimize performance, and automate operations. The following points describe how AI enhances digital twin models:
Predictive Insights
AI algorithms analyze historical and real-time data gathered by the digital twin to identify patterns and trends. For example, machine learning models can predict when a critical component in a manufacturing line might fail which enables maintenance to be scheduled proactively.
By continuously monitoring performance metrics, AI can detect anomalies before they rise into major issues. This early detection helps prevent costly downtime and improves overall reliability.
Advanced Analytics
AI can analyze huge amounts of data from sensors to find hidden patterns and insights that traditional methods might miss. This deep analysis helps create more accurate models of how physical systems work. Advanced algorithms can also simulate different operating situations to let decision-makers test possible changes in a virtual setting. This is especially useful for improving system performance without causing real-world problems.
Automation
Using AI, digital twins can not only suggest corrective actions but also execute them automatically. For example, if a digital twin identifies that a machine is overheating, it might automatically adjust operating parameters or shut the machine down to prevent damage. AI models embedded within digital twins continuously learn from new data. This adaptability means that the system improves its predictive and diagnostic accuracy over time and becomes more effective in managing complex operations.
Imagine a virtual copy of a factory production line. AI tools built into this virtual copy keep an eye on how well the machines are working. If the AI notices a small sign that an important part is wearing out, it can predict that the part might fail soon. The system then changes the workflow to reduce any problems, plans a maintenance check, and gives the repair team detailed information about what’s wrong.
By using digital twin technology with AI, industries can move from reactive to proactive management and transform how they maintain systems, predict issues, and optimize operations.
Digital Twins Examples
Digital twins have many use cases in different domains. Let’s discuss some example of digital twins.
Digital Twin in Spinal Surgery
A digital twin in spinal surgery is a detailed virtual replica of a real surgical operation. It captures both the static setup (like the operating room and patient anatomy) and the dynamic actions (like the surgeon’s movements and tool tracking) in one coherent 3D model. A digital twin is a virtual simulation that mirrors an actual surgery, created by merging data from various sensors and imaging methods.
Digital photograph of a spinal surgery (left) and rendering of its digital twin (right) (Source)
Following are the main components of this digital twin system.
- Reference Frame: A high-precision 3D map of the operating room is built using multiple laser scans. Markers are placed in the room to fuse these scans into one common coordinate system.
- Static Models: The operating room, equipment, and patient anatomy are modeled using photogrammetry (detailed photos) and 3D modeling software. This produces realistic textures and accurate dimensions.
- Dynamic Elements: Multiple ceiling-mounted RGB-D cameras capture the surgeon’s movements. An infrared stereo camera tracks the surgical instruments with marker-based tracking.
- Data Fusion and Integration: All captured data is registered into the same reference frame, ensuring that every element—from the static room to dynamic tools, is accurately aligned. The system is built in a modular and explicit manner, where each component is separate yet integrated.
- Use of AI: AI techniques enhance dynamic pose estimation (e.g., using models like SMPL-H) and help in processing the sensor data. The detailed digital twin data also provides a rich source for training machine learning models to improve surgical planning and even automate certain tasks.
Comparison of the rendered digital twin with the real camera images (Source)
This digital twin can help in the following tasks:
- Training & Education: Surgeons and students can practice procedures in a risk-free, realistic environment.
- Surgical Planning: Doctors can simulate and plan complex surgeries ahead of time.
- Automation & AI: The rich, detailed data can train AI systems to assist with surgical navigation, process optimization, and even automate some tasks.
The digital twin for spinal surgery is a comprehensive 3D virtual model that integrates high-precision laser scans, photogrammetry, multiple RGB-D cameras, and marker-based tracking. This system captures the entire surgical scene and aligns them within a common reference frame. AI plays a role in enhancing dynamic data capture and processing, and the detailed model serves as a powerful tool for training, surgical planning, and automation.
Digital twin in Autonomous Driving
This paper on digital twins in virtual reality describes a digital twin built in a virtual reality setting to study human-vehicle interactions at a crosswalk. The digital twin recreates a real-world crosswalk and an autonomous vehicle using georeferenced maps and the CARLA simulator. Real pedestrians interact with this virtual environment through a VR interface, where an external HMI (GRAIL) on the vehicle provides explicit communication (e.g., changing colors to signal stopping). The system tests different braking profiles (gentle versus aggressive) to observe their impact on pedestrian confidence and crossing behavior. The setup uses questionnaires and sensor-based measurements to collect data, and it hints at leveraging AI for data processing and analysis. Overall, this approach offers a controlled, safe, and realistic way to evaluate and improve communication strategies for autonomous vehicles, potentially enhancing road safety. Following are the components of the system.
Digital twin for human-vehicle interaction in autonomous driving. Virtual (left) and real (right) setting (Source)
- Digital Twin Environment: The virtual crosswalk is digitally recreated using map data to ensure it matches the real-world layout. Experiments run in CARLA, an open-source simulator that creates realistic traffic scenarios.
- Human-Vehicle Interaction Interface: A colored bar on the vehicle indicates if the car is about to stop or yield. Two braking styles are tested which are gentle (slow deceleration) and aggressive (sudden deceleration).
- Virtual Reality Setup: Participants use a VR headset and motion capture to see and interact with the virtual world. Their movements are synchronized with the simulation for accurate feedback.
- Data Collection & Analysis: Participants share their feelings about safety and the vehicle's actions. The system records objective data like distance, speed, and time-to-collision.
- Role of AI: AI analyzes both subjective feedback and sensor data to model behavior and refine communication. AI helps integrate data so the simulation responds realistically to both the vehicle and pedestrians.
This digital twin system helps in following:
- Enhances Safety: Clear communication through the digital twin helps pedestrians understand vehicle intentions, reducing uncertainty and potential accidents.
- Improves Training: It offers a realistic simulation for both pedestrians and autonomous vehicles, enabling safer, hands-on training and evaluation.
- Informs Design: By collecting both subjective feedback and objective measurements, designers can refine vehicle behavior and HMI features for better user interaction.
- Supports Data-Driven Decisions: The system’s real-time data and AI processing allow for continuous improvements in autonomous driving and pedestrian safety strategies.
How Encord Enhances Digital Twin Models
Encord, a data management and annotation platform which can be used in digital twin applications. It is used to annotate, curate, and monitor large-scale datasets to train machine learning models for digital twin creation and optimization. Following are the important points how Encord helps in creating and enhancing Digital Twins.
- Encord provides tools for preparing the data needed to train machine learning models that can power digital twins.
- Encord allows users to annotate and curate large datasets, ensuring the data is clean, accurate, and suitable for training machine learning models that will be used in digital twin applications.
- Encord platform enables users to monitor the performance of their machine learning models and datasets, allowing for continuous improvement and optimization of the digital twin.
- By using high-quality, well-curated datasets, machine learning models can achieve higher accuracy and reliability.
- Encord platform can accelerate the development of digital twins by streamlining the data preparation and model training process.
- Digital twins powered by machine learning models can provide valuable insights into the performance of physical systems, enabling better decision-making.
Key Takeaways
Digital twin technology revolutionizes industrial operations by creating a dynamic virtual replica of physical systems. This technology not only mirrors real-time activities in environments like factories and hospitals but also uses historical data and AI to predict issues, simulate repairs, and optimize processes across various industries.
- Real-Time Monitoring & Visualization: Digital twins provide live, interactive models that replicate every detail of a physical system that allows to quickly identify anomalies and monitor system performance continuously.
- Predictive Maintenance: Digital twin helps in analyzing historical and real-time data which can be used to forecast potential equipment failures and enables proactive maintenance.
- Enhanced Decision-Making Through Simulation: Digital twins allow to simulate repair scenarios and operational adjustments in a virtual space which ensures the most efficient solutions are chosen.
- Cross-Industry Applications: From factory production lines to surgical procedures and autonomous driving, digital twins are transforming how industries plan, train, and optimize their systems.
- AI Driven Insights: The integration of AI and machine learning empowers digital twins to offer advanced analytics, automate corrective actions, and continuously learn from new data to improve accuracy over time.
Data infrastructure for multimodal AI
Click around the platform to see the product in action.
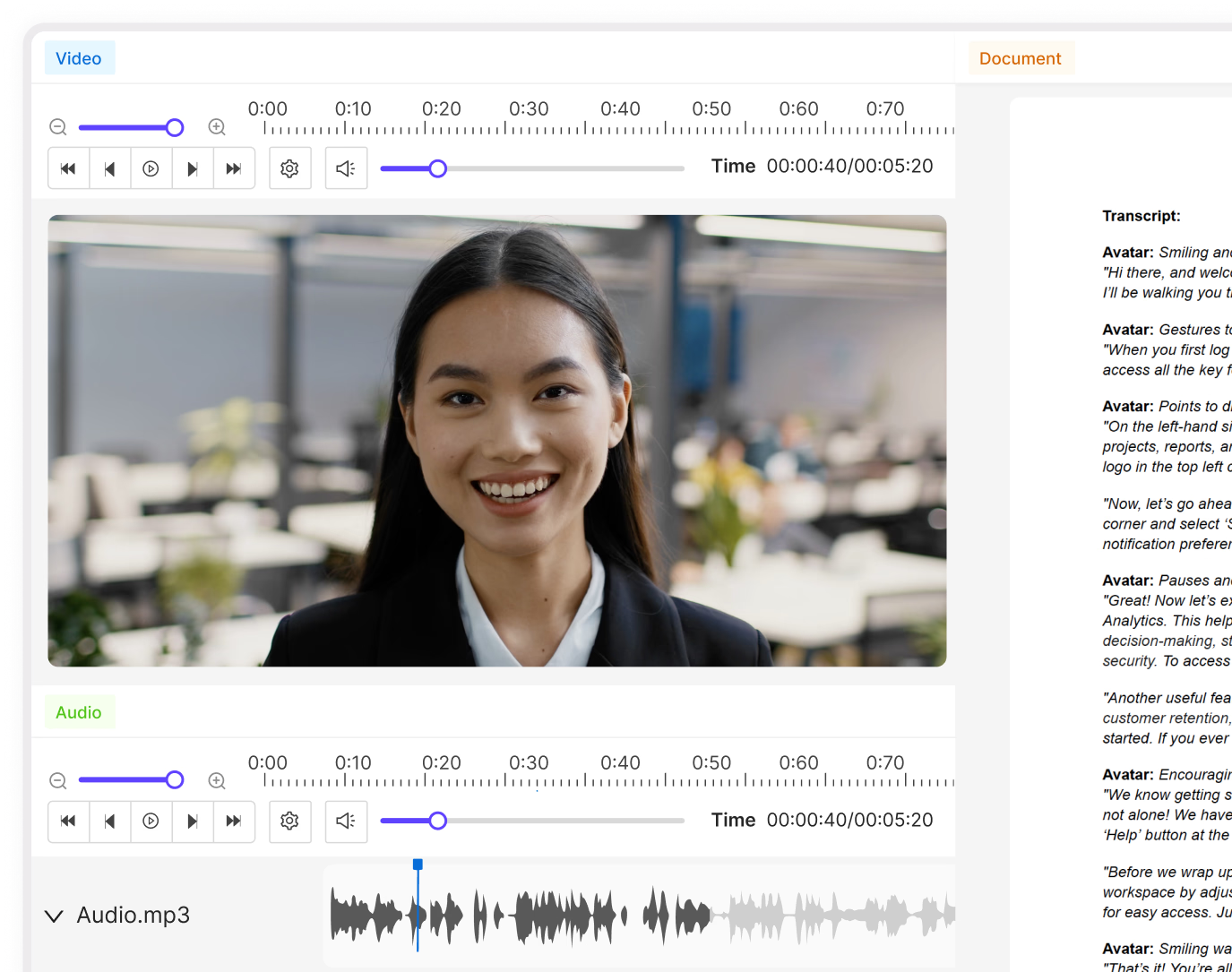
Written by
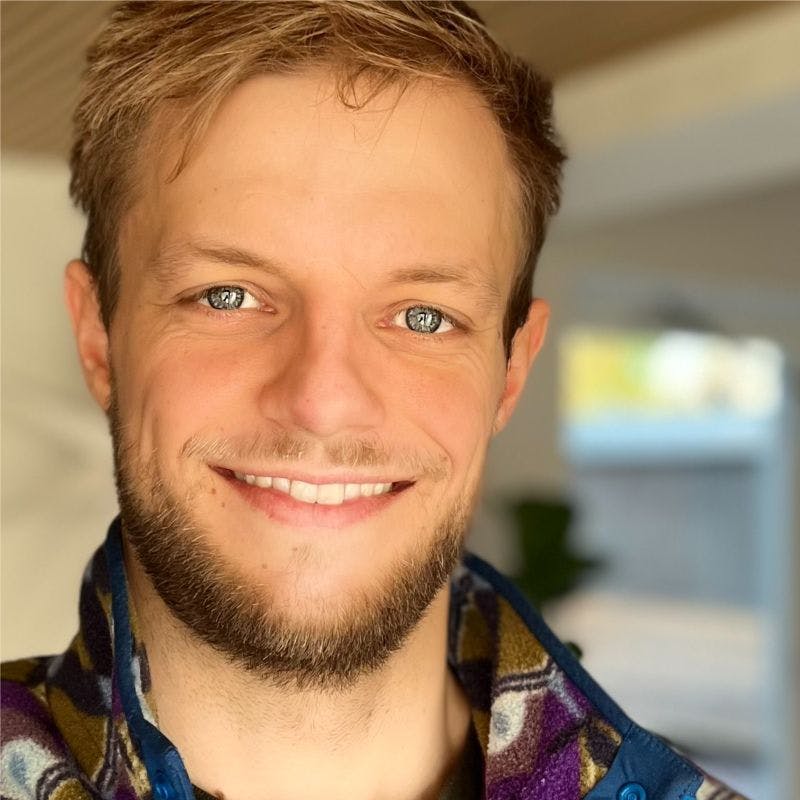
Frederik Hvilshøj
Explore our products
- A digital twin is a real-time, virtual representation of a physical object, process, or system. It uses data from sensors and IoT devices to simulate and monitor real-world performance, enabling improved decision-making and predictive maintenance.
- In a factory, a digital twin replicates machines and workflows using real-time data. Managers can monitor equipment, detect issues, simulate repairs, and optimize performance—all within a virtual environment.
- Component Twins – replicate individual parts. Asset Twins – model entire machines. System Twins – represent interconnected machines or subsystems. Process Twins – model full operational workflows.
- AI improves digital twins by analyzing data for predictive insights, automating responses, and continuously learning from new information to improve performance and accuracy over time.
- Digital twins simulate repair scenarios, operational changes, and process improvements in a risk-free virtual environment, allowing teams to choose optimal strategies before implementing them physically.