Contents
What is Intralogistics?
Use Cases of Internal Logistics
Challenges in Scaling Intralogistics
How Encord Helps Build Intralogistics Tools
Real-World Applications
Conclusion
Encord Blog
Intralogistics: Optimizing Internal Supply Chains with Automation
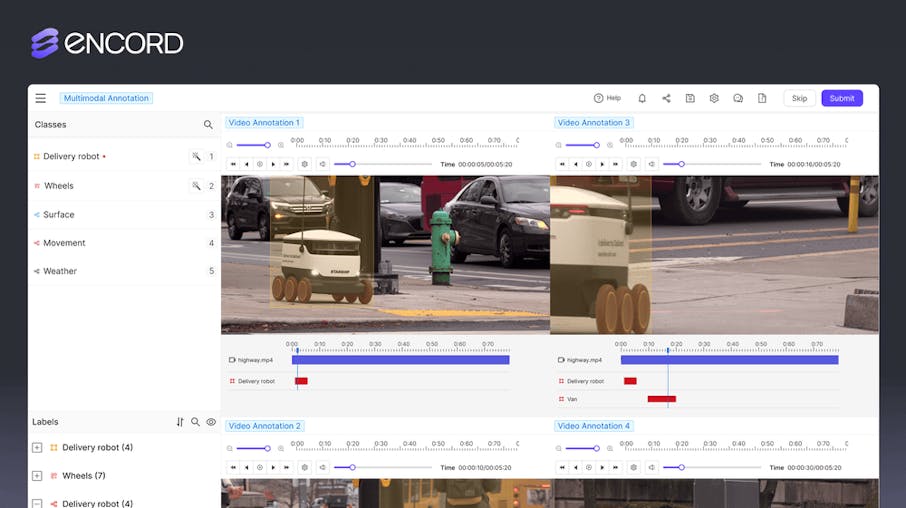
Intralogistics is the backbone of modern supply chains. It ensures a smooth movement of goods within warehouses, distribution centers, and manufacturing facilities. As businesses scale, optimizing internal logistics becomes critical for efficiency, cost reduction, and meeting consumer demands.
With the rise of automation, robotics, and AI-driven logistics, companies are increasingly investing in intralogistics solutions to enhance productivity. But what exactly is intralogistics, and why should organizations care?
What is Intralogistics?
It is the flow of materials, goods, and data within a facility like warehouse, factory, or a fulfilment center. This also includes processes like storage, inventory management, material handling, and order fulfilment.
Traditional logistics focus on external transport systems whereas interlogistics optimizes internal workflows using automation, robotics, and other AI powered systems. Businesses prioritize intralogistics to reduce operational costs, minimize errors, and improve supply chain agility.
Components of Intralogistics
Intralogistics have three core elements:
- Material Flow: The movement of goods within a facility, including receiving, storage, picking, packing, and shipping.
- Data Management: Using real-time data and analytics to provide visibility into inventory levels, order statuses, and equipment performance.
- Warehouse Management: Coordinating warehouse operations from inventory control to space optimization and labor allocation.
Why Intralogistics Matters?
- Efficiency Gains: Streamlining operations improves order accuracy and reduces delays.
- Cost Reduction: Optimized workflows lower labor costs and minimize waste.
- Scalability: AI-driven intralogistics adapts to business growth and fluctuating demand.
- Sustainability: Efficient flow of goods reduces energy consumption and carbon footprint.
Use Cases of Internal Logistics
Warehouse Automation
Warehouses use robots and conveyor belts to transport products faster with fewer mistakes. Autonomous Mobile Robots (AMRs) and Automated Guided Vehicles (AGVs) transport goods, while robotic arms help with picking and packing. The conveyor belts and sortation systems ensure a smooth flow of inventory. AI warehouse management systems (WMS) track inventory in real-time, preventing stockouts and optimizing storage space.
Manufacturing and Production Lines
Factories use conveyor systems to move materials quickly between workstations. Conveyor systems move raw materials through different stages of production with minimal human intervention. Just-in-time (JIT) inventory systems are used to ensure the required parts arrive exactly when needed to avoid delays and also to reduce storage cost. Businesses also use AI models to forecast demands to help manufacturers keep an eye on the stock levels and avoid overstocking.
E-commerce Fulfillment Centers
Online retailers use automated storage and retrieval systems to speed up picking and packing. Automated storage and retrieval systems (AS/RS) organize inventory for fast picking and packing. AI-powered sortation systems classify and route packages efficiently, reducing delivery times. This helps businesses process more orders more efficiently with fewer errors.
Cold Chain Logistics for Pharmaceuticals
Temperature-sensitive goods, like vaccines and perishable medicines, require precise handling. Internal logistics processes, such as IoT-enabled storage systems, monitor temperature and humidity levels in real-time to ensure compliance with regulatory standards. Automated material handling reduces human error and ensures fast, safe transportation of critical healthcare supplies.
Retail and Grocery Distribution
Retailers use automated warehouses to restock shelves quickly. AI helps predict demand, so stores don’t overstock or run out of items.
Challenges in Scaling Intralogistics
Scaling logistical flow internally comes with several challenges, from handling massive amounts of real-time data to integrating automation into legacy systems
Data
Data is at the core of intralogistics. Warehouses, fulfillment centers, and manufacturing plants rely on a huge network of sensors, automation tools, and analytics to optimize product flow. However, managing and processing this data at scale presents several issues:
Real Time Tracking and Visibility
Accurate tracking of inventory, equipment, and shipments is critical for efficient intralogistics. But ensuring real-time visibility is difficult due to:
- Signal Interference: RFID and GPS-based tracking systems often face disruptions in large warehouses, affecting location accuracy.
- Data Latency: Delays in updating inventory counts or shipment status can lead to errors in order fulfillment.
- Scalability Issues: As operations expand, managing a growing network of connected sensors and devices becomes complex.
Data-centric AI can clean and standardize tracking data, improving accuracy by filtering out inconsistencies and detecting anomalies in real time.
Integrating Diverse Data Sources
Intralogistics systems heavily depend on various sensors like RFID scanners, weight sensors, LiDAR, and camera. Each system also interact and rely on data from other systems as well. Hence, integrating and analysing data from these diverse sources presents challenges:
- Inconsistent Data Formats: Different vendors use different data structures, making it difficult to merge information.
- Conflicting Readings: One sensor may detect an object, while another fails to register it, leading to errors in automation.
- Processing Bottlenecks: High volumes of sensor data require powerful computing resources to ensure operational efficiency.
Sensor fusion techniques can align, filter, and cross-validate information, ensuring accurate and consistent data for robotic systems and warehouse automation.
Data Analytics and Decision Making
Handling a large amount of data generated also lead to many challenges:
- Extracting Insights from Raw Data: AI models require well-structured, high-quality datasets for effective decision-making.
- Managing Unstructured Data: Video feeds, IoT logs, and sensor data need to be converted into actionable insights.
- Security and Compliance Risks: Protecting sensitive logistics data from cyber threats while ensuring regulatory compliance adds complexity.
Infrastructure
Many companies operate with legacy warehouse management software (WMS) and enterprise resource planning (ERP) software which are not designed for automation. Integrating new technology with existing infrastructure presents challenges such as:
- Compatibility Problems: Older systems may lack APIs or support for AI tools and robotic automation.
- Scalability Constraints: Expanding automation across multiple facilities requires a standardized approach, which is difficult when working with different vendors.
- Network Reliability: High-speed, stable connectivity is crucial for seamless machine-to-machine communication, yet many warehouses lack the necessary infrastructure.
Specially designed adaptable softwares can be used as an intermediary layer, bridging data gaps between legacy systems and modern automation tools through intelligent API integrations and real-time processing.
Cost and ROI Concerns for Automation
While automation enhances efficiency, the high upfront investment in robotics, AI, and IoT devices raises concerns about the return of investment. The businesses need to consider the following:
- Implementation Costs: AI logistics solutions require significant initial investment in hardware, software, and training.
- Long Payback Periods: Efficiency gains take time to materialize, making it difficult to justify costs in the short term.
- Ongoing Maintenance Expenses: Automated systems require continuous updates and repairs, adding to operational costs.
Still the businesses can leverage AI to optimize automation deployment by identifying high-impact areas for investment. This way businesses can achieve cost savings and efficiency improvements faster.
Workforce Adaptation and Training
As intralogistics systems become more automated, the role of human workers shifts from manual tasks to overseeing and maintaining the automation tools. However, you can face challenges in:
- Upskilling the Workforce: Traditional warehouse workers may lack experience in AI, robotics, and automation, requiring extensive training or hiring the right talent.
- Human-Machine Collaboration: Many intralogistics systems require workers to work alongside AI-driven robots, requiring new skills and training.
How Encord Helps Build Intralogistics Tools
Without accurate, well-labeled data, warehouse robots struggle to detect objects, navigate spaces, or pick and pack items correctly. That’s where Encord comes in. Encord provides a platform to build data centric AI solutions for intralogistics systems.
AI systems for intralogistics are trained on diverse sensor data for warehouse automation, robotic navigation, and quality control. However, training reliable AI models requires accurate, well-labeled datasets. Encord’s data platform enables:
- Automated Video & Sensor Data Labeling: Encord supports video, LiDAR, and multi-sensor data annotation, making it easy to build a robust training dataset to build AI models for warehouse robotics.
- Active Learning for Faster Model Improvement: AI-assisted annotation speeds up dataset creation while improving model accuracy.
- Collaborative Workflow Tools: Teams can manage, review, and scale data labeling efficiently.
- Ensure Continuous Model Optimization: Encord’s platform allows teams to refine datasets over time, improving AI warehouse automation.
Real-World Applications
Here are some of the case studies of large enterprises that have successfully implemented internal supply chain solutions.
Robots in Amazon Fulfilment Centers
Amazon is a prime example of how intralogistics processes can scale operations for massive global demand. It uses AMRs and AMVs in its fulfilment centers for transportation of goods within its warehouses. With over 175 fulfillment centers worldwide, Amazon’s use of intralogistics technology has allowed the company to manage a highly complex network while maintaining quick delivery times, even during peak seasons. The efficiency of the automated system has significantly cut down operational costs and improved order accuracy.
Toyota’s Manufacturing Platform
Along with AGVs in its manufacturing plants to improve warehousing, Toyota also built an AI driven platform which integrates data from various stages of production to improve decision making. By using ML algorithms the platform predicts potential bottlenecks and maintenance issues. This predictive approach reduces downtime and enhances the overall efficiency of production.
Toyota also adopted hybrid cloud solutions to connect its manufacturing facilities globally. This cloud infrastructure allows Toyota to gather real-time data from machines, sensors, and robots across its factories, providing a unified view of its operations.
The integration of AI into its supply chain allows Toyota to predict maintenance needs, optimize the movement of parts with AGVs, and improve production flexibility.
Walmart Improving Distribution with Automation
Walmart, the world’s largest retailer, has long been a leader in logistics innovation. To keep up with its massive scale, Walmart has adopted several intralogistics technologies to optimize its distribution centers and stores.
Automated Sortation and Conveyor Systems
Walmart uses AI sortation systems to process and distribute goods within its distribution centers. The system directs items to the appropriate shipping lanes, speeding up the sorting process.
Robotic Palletizing
Walmart has also experimented with robots, where robotic forklifts are used to stack products onto pallets. This reduces manual labor while maintaining precision, making it easier for Walmart to manage its inventory and prepare orders for shipping.
Conclusion
These real-world examples demonstrate the power of intralogistics in transforming supply chains across various industries. From Amazon’s robotic fulfillment centers to Toyota’s automated manufacturing lines, the adoption of AI, robotics, and automation has allowed businesses to streamline operations, improve accuracy, reduce costs, and scale rapidly. As more companies adopt intralogistics, the future of supply chain management will increasingly depend on technological advancements to drive efficiency and meet the growing customer demands.
Explore our products
- Intralogistics refers to the internal movement and management of goods, materials, and data within warehouses, factories, and fulfillment centers. It includes storage, material handling, and order fulfillment processes.
- Traditional logistics focuses on external transportation of goods, while intralogistics optimizes internal workflows using automation, robotics, and AI-driven systems to improve efficiency and reduce costs.
- Material Flow – The movement of goods within a facility. Data Management – Real-time tracking of inventory and orders. Warehouse Management – Coordinating operations like storage, labor, and automation.
- Common challenges include data integration, real-time tracking, infrastructure limitations, high automation costs, and workforce adaptation to new technologies.
- AI and machine learning improve demand forecasting, automate decision-making, enhance real-time tracking, and optimize robotic workflows for greater efficiency.
- Companies like Amazon, Toyota, and Walmart use AI-driven automation, robotic fulfillment centers, and predictive analytics to optimize their internal logistics and supply chain operations.