Contents
What is Physical AI?
Key Characteristics of Physical AI
Components of Physical AI System
Can AI Have a Physical Form?
Physical AI vs. Embodied AI
The Promise of Physical AI
Data and Hardware Challenges in Physical AI
AI Alignment Considerations
Encord's Role in Advancing Physical AI
Key Takeaways
Encord Blog
What is Physical AI?
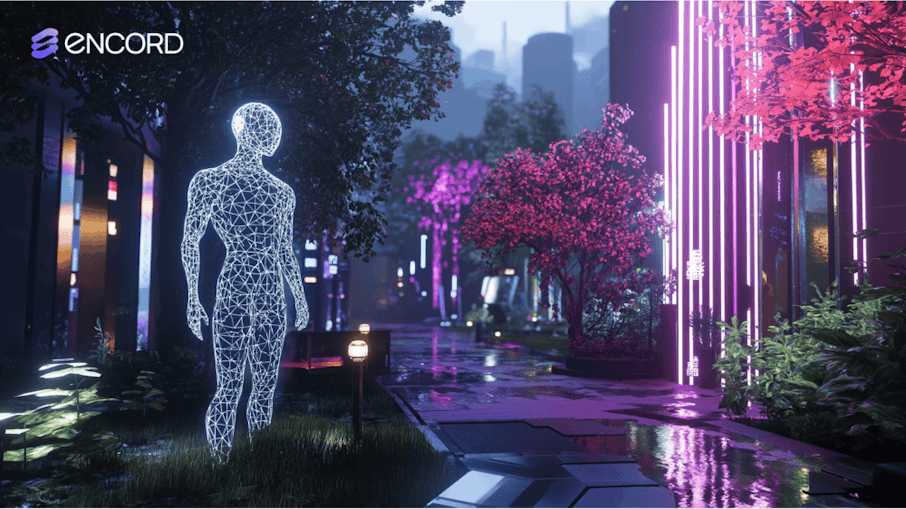
Imagine a world where in the morning the sun rises over busy cities not just with human activity but also with the intelligent machines moving around. A world where your morning coffee is brewed by a robot that not only knows your exact taste preferences but also navigates a kitchen with human-like grace. In this world autonomous delivery drones or robots navigate the urban maze and deliver fresh groceries, essential medicines, and even lunch orders directly to your doorstep. There would also be intelligent robots and drones inspecting cities and assisting in traffic management, taking charge of urban maintenance. Hospitals would have AI-powered robots efficiently deliver medications to patients and warehouses would have robots sort, pack, and ship orders.
This is no longer a science fiction story, it is the emerging reality of Physical AI.
Physical AI illustration by ArchetypeAI (Source)
As projected in the article Nvidia could get a bionic boost from the rise of the robots, Physical AI is the next frontier of artificial intelligence. It is suggested that by 2035, there could be as many as 1.3 billion AI-powered robots operating across the globe. In manufacturing alone, the integration of Physical AI could unlock a multi trillion-dollar market, while advancements in healthcare and transportation promise to dramatically improve safety and efficiency. These statistics underline the enormous potential as well as requirement to harness Physical AI for practical, real-world applications.
Jensen Huang speaking about humanoids during the 2025 CES event (Source)
In this blog, we will deep dive into the world of Physical AI. We'll explore what it is, how it is different from other forms of AI like embodied AI. We will also discuss the data and hardware challenges that need to be overcome and discuss the importance of AI alignment in creating safe systems. We will also explore the role of Encord in Physical AI.
What is Physical AI?
Physical AI refers to the integration of AI (exists in software form), with physical systems. Physical AI enables machines to interact with and adapt to the real world. It combines AI algorithms, such as machine learning, computer vision, and natural language processing, with robotics, sensors, and actuators to create systems that can perceive, reason, and act in physical environments.
Block diagram of the Newton Physical AI foundation model (Source)
Key Characteristics of Physical AI
Following are the key characters of Physical AI.
- Embodiment: Physical AI systems are embodied in physical forms, such as robots, drones, or autonomous vehicles which allow it to interact directly with its surroundings.
- Perception: Physical AI systems make use of sensors (e.g., cameras, microphones, LiDAR) to gather data about their environment.
- Decision-Making: AI algorithms in Physical AI systems process sensor data to make decisions or predictions.
- Action: Actuators (e.g., motors, arms, wheels) enable these systems to perform physical tasks, such as moving, grasping, or manipulating objects.
- Adaptability: Physical AI systems can learn and adapt to new situations or environments over time.
Components of Physical AI System
Physical AI systems integrate hardware, software, and connectivity to enable intelligent interaction with the physical world. The following are the core components:
Sensors
Sensors allow Physical AI systems to see and feel their environment. Sensors help it to collect real-time data enabling the system to understand and respond to external conditions. It can use one or more of the following sensors to understand its surroundings.
Cameras: It is used for computer vision tasks. Cameras capture visual information and allow the system to recognize objects, track movements, and interpret visual cues.
LiDAR/Radar: These sensors emit signals and measure their reflections to create detailed 3D maps of surroundings. These sensors are essential for navigation.
Microphones: It helps capture audio data, enabling the system to process sounds for voice recognition.
Inertial Measurement Units (IMUs): It comprises accelerometers and gyroscopes to track motion, orientation, and acceleration. It also helps in stabilizing the physical body of Physical AI systems.
Temperature, Pressure, or Proximity Sensors: These sensors monitor environmental factors such as heat, force, or distance to nearby objects and allow the Physical AI system to react appropriately to changes.
Actuators
Actuators are responsible for executing physical actions based on the decisions taken by the system in order to enable interaction with the environment. For example, if a robot sees an apple through a camera and receives instruction to pick it up through a microphone, it uses different motors in its arm to plan a path to pick it up. Following are some actuator devices:
Motors: Drive components like wheels or robotic arms assists the movement and manipulation of objects.
Servos: Provide precise control over angular or linear positions which are crucial for tasks requiring exact movements.
Hydraulic/Pneumatic Systems: It uses fluid or air pressure to generate powerful movements and are used in heavy machines or robotic systems requiring significant force.
Speakers: It converts electrical signals into sound to provide audio feedback or communicate with users.
AI Processing Units
The AI processing units handle the intensive computations required for processing sensor data and running AI algorithms to make real-time decisions. Some examples are following:
Graphics Processing Units (GPUs): Specialized for parallel processing, GPUs accelerate tasks like image and signal processing which are essential for real-time AI applications.
Tensor Processing Units (TPUs): Custom-developed by Google, TPUs are designed to efficiently handle machine learning workloads, particularly for neural network computations.
Edge Computing Devices: These processors enable data processing at the source (i.e., on the device itself), reducing latency and reliance on cloud connectivity, which is vital for time-sensitive applications.
NVIDIA Jetson Orin Nano Dk for Edge AI (Source)
Mechanical Hardware
It is the physical components that provide structure to Physical AI and facilitate movement. It provides the tangible interface between the AI system and its environment. The following are some of the examples:
Chassis/Frames: It provides foundational structures to robots, drones, or vehicles and supports all other components of the system.
Articulated Limbs: These are the robotic arms or legs that have multiple joints to allow movements and the ability to perform complex tasks.
Grippers/Manipulators: These are the end-effectors designed to grasp, hold, or manipulate objects. It enables the system to interact physically with various items.
MIRAI AI Enabled Robotic ARM from KUKA (Source)
AI Software & Algorithms
This is the brain of the Physical AI system. It processes the sensor data and helps in making decisions. The key software for Physical AI are as follows.
Machine Learning Models: It is one of the most important parts of Physical AI as it helps the system to understand its environment. It enables systems to learn optimal actions through trial and error.
Robot Operating System (ROS): ROS is the open-source robotics middleware. It is a framework that provides a collection of software libraries and tools to build robot applications and enables hardware abstraction and device control.
Control Systems
The control system translates the decision from AI Software and Algorithm into commands which are executed by actuators. Following are the important control systems:
PID Controllers: PID controller uses proportional, Integral, and derivative calculations for the system outputs such that required for the motion control.
Real-Time Operating Systems (RTOS): RTOS manages hardware resources and ensures real-time execution of tasks. This is very important in Physical AI systems which require precise timing.
Can AI Have a Physical Form?
When most people imagine AI, they think of it as some application, computer programs, or invisible systems like Netflix suggesting a show, Siri answering questions, or chatbots like ChatGPT answering queries. This kind of AI lives entirely in the digital world and works behind the scenes like a ghost that thinks and calculates but it can not move around us and touch and interact with the physical world. In this application, the ai is a software system, like a brain without a body.
Physical AI flips this idea. Instead of being trapped in a computer's memory, the Physical AI gets a body, for example, a robot, self-driving car, or smart machine. Imagine a robot that does not only figure out how to pick up a cup but actually reaches for it, grabs it, and hands it to you. Physical AI connects thinking (algorithms) to real-world action. To do this, it needs:
- Eyes and ears through sensors (cameras, microphones, radar) to see and hear.
- A brain which are the processors to understand what is happening.
- Arms and legs through motors, wheels, or grippers so that it can move and interact.
SenseRobot: AI-Powered Smart Chess Coach and Companion (Source)
Just take an example of a self-driving car, which does not only think about driving but uses cameras to spot stop signs, calculates when to brake, and actually physically presses the brake pedal. Similarly, a warehouse robot that may use AI to find a package, navigate around people, and lift it with mechanical arms.
MARS rover uses AI to identify organic materials in the search for life on Mars (Source)
Why does this matter? Because traditional AI is like a smart assistant on your phone, it can talk or answer queries, but it can not do anything physical. On the other hand, Physical AI can act. It can build things, clean your house, assist surgeons, or even explore Mars. By giving AI a body, we’re turning it from a tool that thinks into a partner that acts. This will change the way we live, work, and solve problems in the real world.
So, we can say that a traditional AI is the brain that thinks, talks, and calculates. Whereas, Physical AI is the brain and the body that thinks, sees, moves, interacts and is possible indeed.
Physical AI vs. Embodied AI
Although Physical AI and Embodied AI seem similar at a glance. They are quite different. Let's understand the difference between the two.
The Physical AI systems are integrated with physical hardware (sensors, actuators, robots etc.) to interact with the real world. The main focus in Physical AI is to execute tasks in physical environments. It combines AI algorithms with mechanical systems and can perform operations such as movement, grasping, navigation. This type of AI relies on hardware (motors, cameras, wheels) to interact with surroundings. An example of Physical AI are self-driving cars that use AI to process sensor data (cameras, radar) and physically control steering, brake, or acceleration. Another example is warehouse robots like Amazon’s Sparrow that use AI to identify, grab, and sort packages.
Embodied AI systems on the other hand are designed to learn and reason through physical interaction with their environment. They focus on intelligence that comes from having a body. The emphasis in Embodied AI is on intelligence that comes from a body’s experiences similar to humans who learn by touching, moving, and interacting. The goal of Embodied AI is to learn skills (e.g., walking, grasping) through trial and error in the real world.
Framework of Embodied Agent (Source)
An example of Embodied AI is Atlas Robot from Boston Dynamics that learns to balance, jump, or navigate uneven terrain by adapting its body movements.
Aspect | Physical AI | Embodied AI |
Focus | Complete specific physical tasks efficiently | Develop understanding through physical interaction |
Intelligence Type | Often uses narrow AI for specific tasks | Aims for more general intelligence through embodied cognition |
Physical Form | May be temporary or interchangeable | Persistent and integral to learning |
Learning Approach | Typically pre-programmed or trained on data | Learns through physical interaction and experience |
Sensory Integration | Uses sensors for specific tasks | Integrates multiple sensory inputs to build body awareness |
Adaptability | Usually task-specific | Can adapt to new situations based on bodily experience |
Hardware Role | Tools to act (e.g., motors) | Body critical to intelligence |
Example | Self-driving, Factory robots, automated warehouse systems, drone navigation systems | Humanoid robots learning to walk, robots that develop motor skills through practice |
We can summarize the difference between the Physical AI is the AI with a body that acts to solve practical problems (e.g., factory automation) and Embodied AI is the AI that needs a body to learn to improve intelligence (e.g., teaching robots common sense through interaction).
The Promise of Physical AI
The promise of Physical AI lies in its ability to bring digital intelligence into the tangible physical world. Physical AI is revolutionizing the way machines work alongside humans and transform different industries. Following are key sectors where Physical AI is set to make a huge impact.
Healthcare
There are many applications of Physical AI in healthcare. For example, surgical robots use AI-guided systems to perform minimally invasive surgeries with precision. Wearable robots such as rehabilitation exoskeletons help patients regain mobility by adapting to their movements in real time. AI powered autonomous robots deliver supplies, sanitize rooms, or assist nurses with repetitive tasks.
Exoskeleton control neural network (Source)
Manufacturing
In manufacturing, collaborative robots (Cobots) are the AI-powered arms that work alongside humans. Cobots learn to handle delicate tasks like assembling electronics or doing more complex tasks that require precision similar to human hands.
Techman AI Cobot (Source)
Agriculture
In agriculture, AI-driven machines plant, water, and harvest crops while analyzing soil health. Weeding robots use computer vision to identify and remove weeds without chemicals and autonomous tractors drive themselves, avoid obstacles using computer vision and other sensor data and perform various farm tasks, from mowing to spraying. These autonomous tractors use sensors, GPS, and artificial intelligence (AI) to operate without a human in the cab.
Driverless tractors perform fully autonomous spraying tasks at a Texas vineyard (Source)
Logistics & Retail
In Logistics & Retail, Physical AI power robots that sort, pack, and deliver goods with speed and accuracy. These robots use real-time decision-making with adaptive learning to handle a variety of products. For example, Proteus robots sort, pack, and move goods autonomously. Other machines like drones or delivery robots (e.g., Starship) navigate to deliver packages.
Amazon Proteus Robot (Source)
Construction
Physical AI has an important role to play in transforming how humans do construction. AI-driven excavators, bulldozers, and cranes operate autonomously or semi-autonomously to perform tasks like digging, leveling, and material placement. Companies like Caterpillar and Komatsu are leveraging AI to create smarter heavy machinery. AI-powered robotic arms can perform repetitive tasks like bricklaying, welding, and concrete finishing with high precision.
Komatsu Autonomous Haulage System (AHS) (Source)
Physical AI is redefining industries by turning intelligent algorithms into real-world action. From hospitals to highways, its ability to act in the physical world will create robots and machines that are not just tools, but partners in solving humanity’s greatest challenges.
Data and Hardware Challenges in Physical AI
The data and hardware challenges in Physical AI revolve around deploying and executing AI models within hardware systems, such as industrial robots, smart devices, or autonomous machinery. This creates some unique challenges related to data and hardware as discussed below.
Data Challenges
Availability of High Quality Data
As with the many other AI systems, this is also an issue with Physical AI. Physical AI systems often require large, precise datasets to train models for tasks like defect detection and path planning etc. These datasets must reflect the exact physical conditions (e.g., lighting, material properties) of the deployment environment. For example, a welding robot needs thousands of labeled images of welds of different metals under various factory conditions and images taken from different angles to train a vision system. Such data is often not available and collecting it manually is costly and time-consuming.
Data Annotation and Labeling Complexity
Physical AI systems require accurately annotated data on a variety of data samples for training which require domain expertise and manual labeling effort. Since the AI must act in real physical condition it must be trained on all possible types of conditions the system may face. For example, training a Physical AI system to detect weld imperfections requires engineers to annotate thousands of sensor readings or images in which labeling error by humans may be possible.
Adapting to New Situations
Physical AI systems are trained on fixed datasets that don’t evolve post-deployment. It may be possible that physical settings (such as change in the environment, place or equipment) in which Physical AI is deployed may change which makes it hard for pre-trained models to work. For example, a robotic arm trained to assemble a specific car model might struggle if the factory switches to a new design. In such cases the model becomes obsolete and requires retraining with fresh data.
Hardware Challenges
Computational Power and Energy Constraints
Running AI models such as deep learning for computer vision on physical hardware requires significant computational resources. Such types of AI models often exceed the capabilities of embedded systems. Battery-powered devices (e.g., IoT sensors) or small robots may also face energy limits and industrial systems need robust cooling. For example, a FANUC welding robot may use a GPU to process sensor data, but integrating this into a compact, energy-efficient unit is costly and generates heat. This may result in hardware failure in a hot environment in the factory.
Sensor Limitations and Reliability
Physical AI depends on sensors (e.g., cameras, LIDAR, force sensors) to perceive the environment. Sometimes these sensors may not give precise reading or fail under harsh conditions (e.g., dust, vibration). Calibrating these sensors repeatedly can also degrade its performance. For example, a camera on a robotic arm may misjudge weld alignment in poor lighting or if dust obscures the lens which leads to defective outputs.
Integration with Legacy Hardware
Many physical systems such as factory robots or HVAC units need modern AI models running on outdated processors or proprietary interfaces. Deploying such AI models into these systems is technically challenging and expensive. For example, upgrading a 1990s-era manufacturing robot to use AI for defect detection may require replacing its control unit which may disrupt the production lines.
Latency and Real-Time Processing Needs
Physical tasks such as robotic welding or autonomous navigation require real-time decision making that must happen in precise milliseconds but AI inference on resource-constrained hardware introduces latency issues. If the AI model is migrated to the cloud, the delays may occur due to network issues. For example, a welding robot adjusting its path in the middle of the welding process might lag if its AI model runs on a slow CPU which results in uneven welds.
AI Alignment Considerations
The AI alignment problem refers to the challenge of ensuring that AI systems act in ways that are aligned with human values, goals, and ethical principles. This problem becomes especially critical as AI systems become more capable and autonomous. The misaligned AI could potentially cause harm, either unintentionally or due to conflict in objectives.
In the context of Physical AI the alignment problem takes on additional layers of complexity as AI systems interact with the physical world. Following are the key alignment problems related to physical AI.
Real-World Impact
Physical AI systems have direct impact in the physical world. Misalignment in these systems can lead to physical harm, property damage, or environmental disruption. For example, a misaligned autonomous vehicle might prioritize efficiency over safety but it may sometimes lead to accidents. Therefore, ensuring that physical AI systems understand and respect human intentions in real-world environments is a significant challenge.
Unpredictable Environments
Physical AI operates in environments that are often unpredictable and complex. This makes it harder to train such AI models in all possible scenarios. This increases the risk of unintended behavior. For example, a household robot may misinterpret a human’s command in a way that leads to dangerous actions, such as mishandling objects or entering restricted areas.
Ethical and Social Considerations
Physical AI systems often operate in shared spaces with humans which can raise ethical questions about privacy, consent, and fairness. Misalignment could lead to violations of these principles. For example, a surveillance robot may overstep boundaries in monitoring public spaces which can lead to privacy concerns especially in areas like international boundaries between two countries.
The AI alignment problem in Physical AI is not just about getting the AI algorithms right but it's also about integrating intelligence into machines that interact safely and beneficially with the physical world.
Encord's Role in Advancing Physical AI
Encord plays an important role in advancing Physical AI by enabling developers with the tools needed to efficiently manage and annotate multimodal data for training models. Accurately annotated data is essential for training intelligent systems that interact with the physical world. In Physical AI, robots and autonomous systems rely on a variety of data streams in the form of high-resolution images and videos to sensor readings like LiDAR and infrared to understand their environments and make decisions. Encord platform enables the process of annotating and curating this heterogeneous data and ensures that the AI models are trained on rich, accurate datasets that capture the complexities of real-world environments.
For example, consider the customer story of Four Growers. Four Growers is a robotics and AI company that creates autonomous harvesting and analytics robots for agriculture, starting in commercial greenhouses. Four Growers uses multimodal annotation capabilities of Encord to label vast amounts of agricultural imagery and sensor data collected via drones and field sensors. This annotated data is then used to train models that power robots capable of precise crop monitoring and yield prediction. The integration of such diverse data types ensures that these AI systems can adapt to varying lighting conditions, detect changes in crop health, and navigate complex field terrains which are all critical for automating agricultural processes and optimizing resource management.
Tomato Harvesting Robot by Four Growers (Source)
The robot uses high-resolution images and advanced sensors to capture the detailed spatial data across the field. This information is used to create yield heatmaps that offer a granular view of crop performance. These maps show fruit count and yield variations across different parts of the field.
When the robot is harvesting, its AI model helps in identifying and localizing tomatoes among the plant but also analysing its ripeness. By detecting the current ripeness and growth patterns, the system predicts how many tomatoes will be ripe in the coming weeks. Encord helps in the annotation and processing of multimodal data to train this kind of Physical AI system.
Tomato Yield Forecasting (Source)
Encord helps to accelerate the development of robust AI models for Physical AI by providing tools to prepare high-quality, multimodal training datasets. Whether it’s in agriculture, manufacturing, healthcare, or urban management, Encord platform is a key enabler in the journey toward smarter, safer, and more efficient Physical AI systems.
Key Takeaways
Physical AI is transforming how machines interact with our world by integrating AI into physical systems like robots, drones, and autonomous vehicles. Following are the key takeaways from this blog:
- Physical AI uses AI with sensors, processing units, and mechanical hardware to enable machines to understand, learn, and perform tasks in real-world environments.
- Physical AI focuses on executing specific tasks in the real-world, whereas Embodied AI emphasizes learning and cognitive development through physical interactions imitating human experiential learning.
- Physical AI is set to revolutionize industries by automating complex tasks, improving safety and efficiency, and unlocking multi-trillion-dollar markets.
- Successful deployment of Physical AI depends on overcoming data quality, hardware constraints, sensor reliability, and ethical AI alignment challenges.
- Encord offers powerful tools for annotating and managing multimodal data to train Physical AI.
Explore our products
- Physical AI is artificial intelligence integrated with physical systems like robots, drones, and self-driving cars. It allows machines to perceive, reason, and interact with the real world, enabling them to perform physical tasks autonomously.
- Traditional AI exists in software form, making decisions and predictions without interacting with the physical world (e.g., ChatGPT, Netflix recommendations). Physical AI, on the other hand, has a physical form and uses sensors, actuators, and control systems to move and manipulate objects in real-world environments.
- No, they are related but different. Physical AI focuses on performing physical tasks efficiently, while Embodied AI is about learning and improving intelligence through physical interaction, similar to how humans learn through experience.
- Physical AI is transforming healthcare, manufacturing, agriculture, logistics, retail, and construction. Examples include surgical robots, autonomous tractors, warehouse robots, and AI-powered factory automation.