Contents
Understanding 6 Degrees of Freedom (6 DoF) of Robotic Arms
Vision-based Control: An Overview
Vision-based Control Techniques
Implementing Vision-Based Control in a 6 DoF Robotic Arm
Real-world Applications of Vision-Based Control in a 6 DoF Robotic Arm
Challenges of Vision-Based Control in a 6 DoF Robotic Arm
Vision-based Control of Robotic Arm: What’s Next?
Vision-based Control of Robotic Arm: Key Takeaways
Encord Blog
Exploring Vision-based Robotic Arm Control with 6 Degrees of Freedom
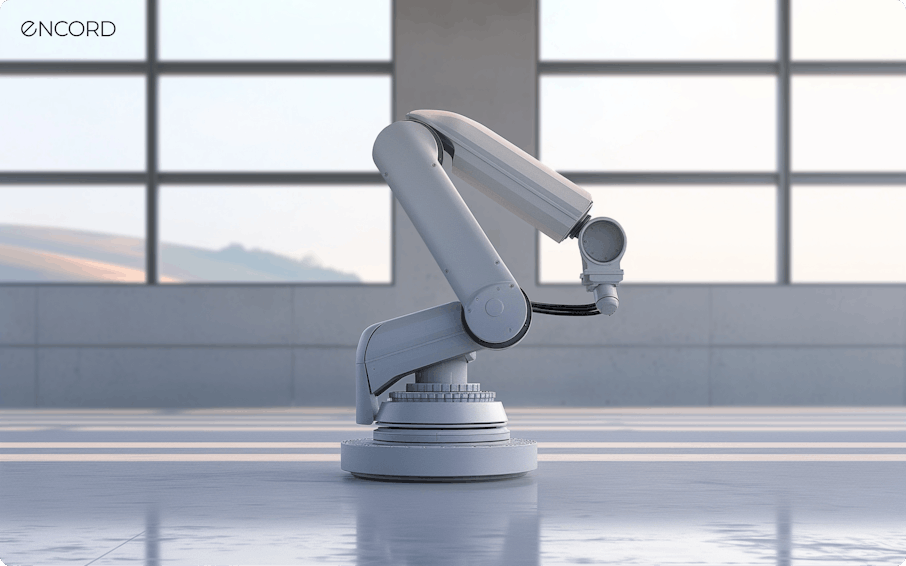
Robotic arms can be found in various industries, from manufacturing and assembly to healthcare and space exploration. These machines have the ability to perform complex tasks with precision and are often deployed in environments that are hazardous or inaccessible to humans. However, traditional robotic arm control methodology, which relies on predefined trajectories or joint-level commands, can be limited in their adaptability and responsiveness to dynamic environments.
Vision-based controls are used to overcome this obstacle. Computer vision techniques are used to enable the robotic arms to perceive their surroundings and respond accordingly. By integrating vision feedback, robotic arms can adapt to changes in their environment, track moving objects, and navigate complex scenarios with increased flexibility and autonomy.
Here we will discuss:
- Understanding robotic arms
- Vision based control of robotic arms and its benefits
- Vision based control techniques
- proposed method for Implementing Vision-Based Control in a 6 DoF Robotic Arm
- Practical applications
- And its challenges.
Understanding 6 Degrees of Freedom (6 DoF) of Robotic Arms
Robotic arms are characterized by their degrees of freedom (DoF), which determine the range of motion and dexterity they possess. The term "degrees of freedom" refers to the independent movements or axes along which a robotic arm can move. A 6 DoF robotic arm is capable of moving in six independent directions, allowing for a broad range of positioning and orientation possibilities.
The 6 DoF in a robotic arm can be broken down into two distinct categories in the cartesian coordinate system -
Positioning (3 DoF):
- Linear movement along the X-axis (left/right)
- Linear movement along the Y-axis (forward/backward)
- Linear movement along the Z-axis (up/down)
Orientation (3 DoF):
- Rotation around the X-axis (roll)
- Rotation around the Y-axis (pitch)
- Rotation around the Z-axis (yaw)
Categorization based on Cartesian Coordinates - 6 DoF Robotics Arm
With these six independent movements, a 6 DoF robotics arm can reach virtually any point within its workspace and orient itself in any desired direction. This mimics the dexterity of human arms, enabling them to perform tasks that were previously challenging for traditional robots with fewer degrees of freedom.
Vision-based Control: An Overview
Vision-based control, also known as visual servoing, is a technique in robotics where feedback from vision sensors is used to control the movement of a robot. This approach is particularly useful for robotic arms, which often need to interact with their environment in a precise and flexible manner.
The main advantage of vision-based control is that it allows the robot to respond to changes in its environment in real-time. This is important in many applications, such as assembly tasks, where the robot needs to adapt to variations in the position and orientation of the parts.
Watch the latest video of Boston Dynamics’ humanoid robot using computer vision to pick up a target object and place it at the target location.
Vision-based control systems typically consist of a camera (or multiple cameras) that provides visual feedback, a processing system that interprets this feedback, and a control system that uses this information for the optimization of the mobile robot’s movements.
Vision-based Control Techniques
There are several common approaches to vision-based control, each with its own strengths and weaknesses:
Position-Based Visual Servoing (PBVS)
In PBVS, the 3D position of the object relative to the camera is estimated and used to control the robot. The goal is to minimize the error between the current and desired position of the object in the camera frame. This requires a good model of the camera and the object, and it can be sensitive to errors in the model or the position estimation.
Image-Based Visual Servoing (IBVS)
IBVS directly uses the image coordinates of the object to control the robot. The goal is to minimize the error between the current and desired position of the object in the image. This approach can be more robust to model errors, but it can also be more challenging to implement due to the non-linear relationship between the image coordinates and the robot’s movements.
Hybrid Visual Servoing
This approach combines elements of PBVS and IBVS. It uses both the image coordinates and the estimated 3D position of the object to control the robot. This can provide a good balance between robustness and precision.
2D/3D Visual Servoing
This approach uses a 3D model of the object along with a 2D image dataset to control the robot. This can provide high precision and flexibility, but it is dependent on image processing techniques, and the rendered 3D model of the object, and hence can be computationally intensive.
Deep Learning-Based Visual Servoing
This is a more recent approach that uses machine learning techniques to learn the relationship between the image data and the robot’s movements. This can be very flexible and adaptive but requires a large amount of training data and can be computationally intensive.
Implementing Vision-Based Control in a 6 DoF Robotic Arm
Implementing vision-based control in a robotic arm with 6 Degrees of Freedom (6DoF) involves several steps. Here’s a general overview of the process:
Sensor Setup
The first step is to set up the vision sensor (usually a camera) in a position where it can clearly see the workspace of the robotic arm. The sensor should be calibrated to ensure accurate measurements.
Object Detection and Tracking
The vision system needs to be able to detect and track the objects that the robotic arm will interact with. This can be done using various computer vision techniques, such as color-based detection, shape-based detection, or machine learning-based detection.
Motion Planning
The vision system determines the desired position and orientation of the end effector based on the visual feedback. This could be the position of an object to be picked up by the gripper, a location to move to, or a path to follow.
Control Algorithm Implementation
The control algorithm uses the desired position and the end effector's current position to calculate the robotic arm's necessary movements. This is where the specific vision-based control techniques (PBVS, IBVS, etc.) or neural networks are implemented.
Inverse Kinematics Calculation
The control commands calculated by the control algorithm are in the form of a desired position and orientation for the end effector. The Inverse Kinematics (IK) process is used to convert this into joint angles that can be applied to the robotic arm.
Control Command Execution
The calculated joint angles are sent to the motors of the robotic arm, allowing it to move. The vision system continues to track the end effector and the object, providing continuous feedback for the control system.
Error Correction
The vision system checks the result of the movement and calculates any error between the desired and actual position of the end effector. This error is fed back into the control algorithm for validation and to correct future movements.
This process continues in a loop, allowing the robotic arm to respond in real-time to changes in its environment.
Real-world Applications of Vision-Based Control in a 6 DoF Robotic Arm
Precision Manufacturing
In industries such as automotive, aerospace, and electronics, the accuracy and precision of assembly is very important. A 6 DoF robotic arm, equipped with a vision system, can identify, pick, and place components with high precision and speed.
Medical Applications
In the medical field, vision-based control in a 6 DoF robotic arm has great potential. For instance, in surgical procedures, a 6 DoF robotic arm can assist surgeons in performing complex operations with high precision. The vision system can provide real-time imaging of the surgical area, enabling the robot to make precise movements and adjustments based on the surgeon’s commands.
Moreover, in rehabilitation therapy, a 6 DoF robotic arm can help patients regain motor skills. The vision system can monitor the patient’s movements and provide feedback to the robot, allowing it to adjust the therapy program dynamically.
Applications in Space
In space missions, a 6 DoF robotic arm with vision-based control can be used for berthing applications. The robotic arm can assist in docking spacecraft together in orbit. The vision system can identify docking ports and guide the robotic arm to align and connect the spacecraft accurately. This is particularly useful in constructing and maintaining large structures in space, such as the International Space Station.
Inspection and Quality Control
In manufacturing industries, a 6 DoF robotic arm with vision-based control can also be used for inspection and quality control. The vision system can inspect the manufactured products for defects, and the robotic arm can remove the defective products from the production line. This ensures that only high-quality products reach the customers.
Search and Rescue
The robotic arm can navigate through difficult terrains and tight spaces, and the vision system can help locate the victims. This can significantly improve the efficiency and effectiveness of search and rescue operations.
These are just a few examples of the many real-world applications of vision-based control in a 6 DoF robotic arm. As technology continues to advance, we can expect to see even more innovative uses of this versatile robotic system.
Challenges of Vision-Based Control in a 6 DoF Robotic Arm
Lighting Conditions
One of the significant challenges in vision-based control is dealing with varying lighting conditions. Changes in light intensity and direction can affect the robot’s ability to accurately identify and locate objects. This is particularly problematic in outdoor environments where lighting conditions can change rapidly.
Occlusion
Occlusion is another challenge in vision-based control. If an object of interest is partially or fully blocked by another object, the vision system may not be able to accurately identify or locate it. This can affect the robot’s ability to perform tasks such as picking and placing objects.
Real-Time Processing
Vision-based control requires real-time processing of visual data to guide the robot’s movements. This can be computationally intensive, particularly when dealing with high-resolution images or complex environments. It requires powerful processors and efficient algorithms to ensure timely and accurate control.
Calibration
The vision system and the robotic arm need to be accurately calibrated to ensure precise control. Any errors in calibration can lead to inaccuracies in object identification, location, and robot movements. Calibration can be a complex and time-consuming process, particularly for 6 DoF robotic arms that have multiple joints and degrees of freedom.
Vision-based Control of Robotic Arm: What’s Next?
Advanced Machine Learning Algorithms
Machine learning algorithms play an important role in vision-based control systems as we saw above. They enable the robot to learn from experience and improve its performance over time. In the future, with the increase in robust vision language models, we can expect to see more advanced machine learning algorithms that can handle complex tasks with greater accuracy and efficiency.
Improved Sensor Technology
The quality of the vision system depends largely on the quality of the sensors. Future advancements in sensor technology could lead to more accurate and reliable vision systems. This could include sensors that can capture more detailed images, work in a wider range of lighting conditions, or even detect other properties such as temperature or pressure.
Integration with Other Technologies
Vision-based control systems could be integrated with other technologies to enhance their capabilities. For example, they could be combined with haptic feedback systems to allow the robot to feel the objects it is manipulating. This could enable more delicate and precise movements.
Greater Autonomy
As vision-based control systems become more sophisticated, we can expect to see robotic arms that can operate with greater autonomy. This could include the ability to plan and execute complex tasks without human intervention, or to adapt to unexpected changes in the environment.
Vision-based Control of Robotic Arm: Key Takeaways
- 6 Degrees of Freedom (6 DoF) Robotic Arms: Offering high dexterity, these arms mimic human versatility, crucial for precise tasks.
- Vision-based Control: Using feedback from vision sensors, robotic arms adapt in real-time, enhancing responsiveness.
- Real-world Applications: From precision manufacturing to space exploration, vision-based control enables tasks in diverse fields, improving efficiency and safety.
- Challenges and Future Directions: Overcoming lighting variations, occlusion, and real-time processing challenges pave the way for future advancements like improved sensors and the use of artificial intelligence.
Explore our products
- The six degrees of freedom (DoF) for a robot arm refer to the independent movements it can make. They include three translations (moving up/down, left/right, forward/backward) and three rotations (around the X, Y, and Z axes).
- The number of degrees of freedom a robot should have depends on its intended tasks. More complex tasks require more degrees of freedom. Robotic arms typically range from three to seven degrees of freedom or more.
- A robotic arm with 6 DoF can move in six different directions: up/down, left/right, forward/backward, and can rotate around the X, Y, and Z axes.
- The 6 DoF actuators in a robot arm are typically the motors or servos that control each joint of the arm, allowing it to move in six different directions.
- Yes, deep reinforcement learning (DRL) can be applied to develop vision-based control algorithms for 6-DoF robotic arms. DRL enables the robotic arm to learn complex tasks through trial and error, based on visual feedback from its environment.
- Visual servoing can be applied to control a 6-DoF robotic arm by using camera feedback to adjust the arm’s movements in real-time, ensuring accurate positioning and orientation.
- Challenges in implementing vision-based navigation and control for a 6-DoF robotic manipulator include dealing with dynamic and unstructured environments, ensuring system accuracy and stability, and handling uncertainties in kinematic and dynamic parameters.
- Yes, an RGB camera can be used for data collection in a visual servo system for a 6-DoF robot arm. It can provide visual feedback for the system without requiring calibration in the sensor frame.