Contents
Types of Automated Guided Vehicles
How Automated Guided Vehicles Operate?
Automated Guided Vehicles: Applications in Warehousing
Benefits and Challenges of AGVs
How Computer Vision Can Enhance AGVs?
Automated Guided Vehicles (AGVs): Key Takeaways
Encord Blog
Automatic Guided Vehicles: The Future of Machine Vision in Warehousing
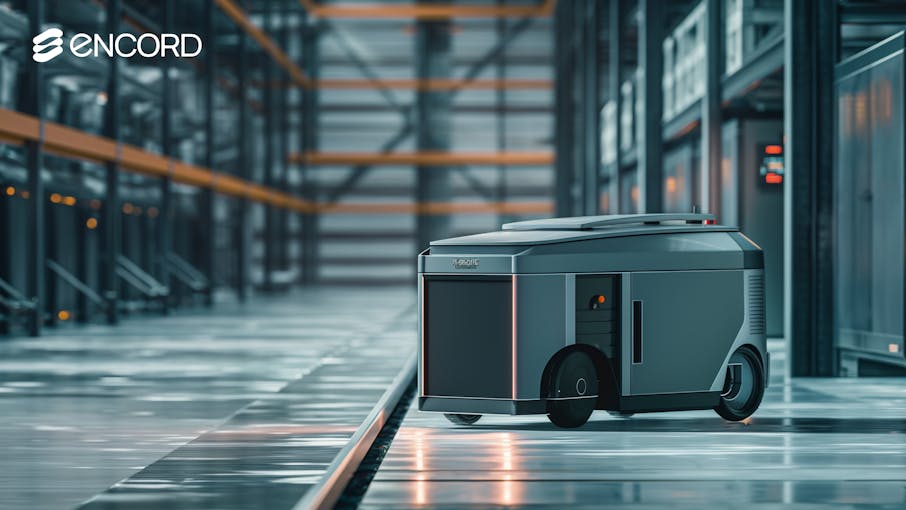
Warehouse automation is no longer a luxury but a necessity for businesses striving to stay competitive in today’s fast-paced markets. With most of the market facing a 25% staff shortage for filling in material handling positions, automation is now the key to unlocking productivity gains.
One popular example is how businesses use automated guided vehicles (AGVs) on warehouse floors to manage inventory and deliver finished goods to the desired destination.
AGVs are self-guided vehicles that handle material and carry loads around warehouses and distribution sites without requiring a human driver. Due to their versatility and cost-saving potential, experts predict the AGV market will grow by 7% annually between 2024 and 2032.
In this article, we will discuss the types of AGVs, how they work, their applications in a warehouse, their benefits and challenges, and the role of machine vision technology in enhancing these autonomous carriers.
Types of Automated Guided Vehicles
With AGV systems becoming increasingly common in manufacturing facilities, knowing the different AGV types is crucial to implementing the right variant for your use case.
Below, we discuss seven AGV variants, including
- Automated Guided Carts (AGCs)
- Forklift AGVs
- Unit-Load AGVs
- Heavy-Burden Carriers
- Hybrid AGVs
- Autonomous mobile robots (AMRs)
Automated Guided Carts (AGCs)
AGCs are the simplest type of AGV with the most basic functionality. They move through paths using a magnetic tape navigation system. The cart helps transport small items, including parts for the assembly line. It also helps with sorting, storage, and cross-docking workflows.
One popular use case involves transporting materials like food items, sterile medical instruments, and linens across hospital floors. The method reduces labor costs by using AGCs instead of human staff.
Forklift AGVs
Forklift AGVs are similar to conventional forklift trucks, but the only difference is that they require no human intervention. They can lift heavy loads to multiple heights and help supply raw materials to production lines.
Forklift Automated Guided Vehicles (AGV)
They also function as retrieval systems by carrying items to and from racks and improving warehouse operations by transporting goods to distribution centers.
Unit-Load AGVs
Unit-loadAGVs help transport individual items, such as pallets, containers, and racks. They can carry loads weighing up to 20 tons and offer significant flexibility in transporting items to and from fixed conveyors.
Unit-load Automated Guided Vehicles (AGV)
The vehicles increase operational efficiency in distribution centers and manufacturing facilities by automating loading and unloading processes.
Transbotics, a brand by Scott, offers multiple unit-load AGV types for handling pallets and racks. Similarly, America in Motion sells high-quality unit-load AGVs with a modular design tailored to capacity requirements.
Towing AGVs
Manufacturers use towing AGVs to pull other manual load-carrying vehicles in a train-like fashion to transport heavy items over long distances.
The automated system has a coupling method to connect with other vehicles. The vehicles navigate a predefined path with multiple pick-up and drop-off locations.
Towing Automated Guided Vehicles (AGV)
MasterMover is a well-known brand that provides a variety of electric tugger vehicles of different weights and sizes. CEIT is another towing AGV manufacturer offering products with significant scalability and customizability.
Heavy Burden Carriers
Heavy-burden carriers transport the heaviest loads, including large plates, coils, assembly components, and castings, to enhance warehouse automation.
These autonomous vehicles often have self-loading features and complex steering functionalities to navigate small, narrow spaces. Steering can be standard, pivotal, or omnidirectional.
Pack Mule offers sturdy burden carriers that can withstand loads of up to 5000 lbs. Green Valley is a reliable manufacturer of burden carriers for transporting heavy-duty industrial equipment.
Hybrid AGVs
Hybrid AGVs consist of automatic and manual components. Manufacturers can use them autonomously or have a human operate them on the warehouse floor.
Processes that require adaptability for material handling benefit significantly from hybrid AGVs. These vehicles offer manufacturers much flexibility in tailoring operations to their requirements.
Hybrid Automated Guided Vehicles (AGV).
Casun is an innovative manufacturer of hybrid AGVs with auto-charging and an intelligent traffic control system. Similarly, Jungheinrich—a Mitsubishi Caterpillar Forklift America brand—offers a hybrid tow tractor that can carry multiple trailers with precise navigation.
Autonomous Mobile Robots (AMRs)
With recent advancements in machine vision, AMRs are sophisticated autonomous systems that use sensor technology to navigate paths.
They consist of artificial intelligence (AI), machine learning (ML), and computer vision (CV) algorithms that understand their surroundings in real-time for collision avoidance and dynamic navigation.
Autonomous Mobile Robots (AMRs)
The technology allows AMRs to automatically define their routes and adjust their paths according to their environment.
Conveyco offers state-of-the-art AMRs for moving inventory, sorting, and picking. Also, ABB provides AMRs for multiple use cases, including tugging, carrying heavy loads, and handling pallets.
How Automated Guided Vehicles Operate?
AGV technology involves a few complex operational mechanisms. Understanding how they work will allow manufacturers to maximize scalability, safety, and uptime.
The following sections discuss four components of AGVs that play an important role in their operational efficiency: navigation, steering, traffic control, and battery charging.
Navigation
Multiple systems help guide AGVs on the warehouse floor. The list below discusses seven methods: wired, tape, laser target, inertial navigation, vision guidance, geo-guidance, and light detection and ranging (LiDAR) navigation systems.
- Wired: AGVs follow a wired path that sends them signals through sensors. The signals guide AGVs throughout the embedded wired path.
- Tape: A magnetic tape installed on the warehouse floor guides AGVs using magnetic sensors.
- Laser Target: AGVs with laser navigation technology emit laser beams that bounce off reflectors placed on the warehouse floor. AGVs detect the reflected beams to compute their current location.
- Inertial Navigation: Inertial navigation uses gyroscopes and accelerometers to guide AGVs along a particular path.
- Vision Guidance: Advanced sensors and cameras detect invariant features along a path, allowing AGVs to recognize obstacles for dynamic navigation.
- Geo-guidance: AGVs detect objects in real-time to calculate their current location and move throughout the warehouse floor.
- LiDAR: LiDAR technology uses laser pulses emitted from sensors to calculate the distance between an object and the vehicle. The pulses help build a 3-dimensional map of the environment, which the vehicles use for navigation.
AGV Steering
Steering systems in AGVs help with maneuverability around objects and narrow paths. Common steering methods include differential speed control, steering wheel control, or both.
- Differential Speed Control: This is the most common steering method. It uses two drive wheels for turning and moving forward or backward. When turning, the drive wheels operate at different speeds, with the same speed for back-and-forth motion. The method is unsuitable for towing vehicles and mostly occurs in AGVs operating near machines.
- Steered Wheel Control: This method is more precise than differential speed control. It uses a single steering wheel to turn like a normal car. It is ideal for applications where AGVs have to follow a pre-programmed path. However, it is less flexible than differential speed control.
- Combination Steering: Combination steering involves two independent drive motors on the diagonal corners and swiveling castors on the other two. The mechanism allows AGVs to turn in any direction and use differential steering mode when needed.
AGV Traffic Control
Traffic control systems prevent AGVs from colliding with other objects and ensure vehicle safety. Common methods include zone control, collision avoidance, and combination control.
- Zone Control: A wireless transmitter sends signals to sensors installed in AGVs in particular areas. The signals tell AGVs whether the path is clear for the AGV to enter or pass through. The transmitter also signals other AGVs to stop if another AGV passes through. The waiting AGVs only move when the transmitter sends a signal indicating a clear path.
- Collision Avoidance: AGVs use sensors to transmit signals and wait for a response to detect obstacles. Sensors can be sonic, optical, or infrared.
- Combination Control: Combination control uses zone control and collision avoidance sensors for a robust control system. The AGVs may use zone control sensors as their primary traffic control mechanism but have collision sensors as a backup.
Battery Charging
Modern AGVs allow users to choose from three battery charging options: batter swap, automatic and opportunity charging, and automatic battery swap.
- Battery Swap: A human operator must manually change a discharged battery with a charged one every 8 to 12 hours.
- Automatic and Opportunity Charging: With automatic charging, AGVs get a charge every 12 minutes, requiring no human intervention. In contrast, opportunity charging occurs whenever the battery charge reaches a predetermined level, and the AGV finishes a current job. It automatically reaches the charging station for battery recharge.
- Automatic Battery Swap: An automatic battery swap is similar to a manual battery swap, with the only difference being that the system uses automatic battery changers to replace discharged batteries.
Automated Guided Vehicles: Applications in Warehousing
Modern manufacturing systems rely heavily on automatic systems to reduce costs and minimize accidents. AGVs offer a viable solution to manufacturers by automating transportation and material handling processes.
Below are a few AGV use cases that help manufacturers efficiently manage warehouses and inventory workflows.
- Transportation of Raw Materials: AGVs help replace conveyors for transporting raw materials such as metal, paper, and plastic to storage facilities or production sites.
- Work-in-Process (WIP): WIP is a significant component of manufacturing processes and requires transportation from one workstation to another. AGVs automate these movements between workstations, increasing production efficiency across all stages.
- Finished Goods Handling: Careful handling of finished goods is vital to avoid costly damages. AGVs transfer finished goods to distribution sites, offering additional safety and security.
- Pallet Handling: Pallet handling is a repetitive process in a manufacturing environment, and AGVs automate these movements from palletizers to shipping sites.
- Trailer Handling: AGVs help load materials directly onto outbound road trailers, requiring no manual input.
- Roll Handling: Manufacturers use AGVs to transport rolls found in paper and still mills, printers, and newspaper plants. Autonomous vehicles can carefully lift, stack, and store these rolls at relevant storage sites.
Benefits and Challenges of AGVs
While the sections above highlight how AGVs help optimize manufacturing processes, it is crucial to understand their benefits and challenges in more detail.
Knowing the benefits will allow manufacturers to understand in what areas AGVs maximize operational efficiency, increase safety, and provide the greatest competitive advantages.
Similarly, learning about the challenges will help manufacturers understand implementation costs, potential technical issues, staff requirements to manage infrastructure, and scalability constraints.
Benefits
- Reduce Labor Costs: Since AGVs automate repetitive and tedious tasks, implementing them helps manufacturers save significantly on labor costs. Instead, they can assign the workforce more productive tasks for better warehouse management.
- Enhanced Workplace Safety: Working in warehouses involves physically demanding tasks such as lifting heavy items, carrying toxic material, and moving extensively between workstations. Performing these tasks manually exposes the workforce to several safety hazards. AGVs improve workplace safety by performing these tasks automatically without any human input.
- Speed and Accuracy: AGVs perform tasks with much greater accuracy and speed than manual labor. Their calculated movements and precise material handling mechanisms allow them to avoid errors that may occur with manual work.
Challenges
- Inappropriate for Non-repetitive Tasks: AGVs are unsuitable for tasks requiring human judgment. AGVs are only appropriate for jobs that have a repetitive nature with pre-programmed steps.
- Less Operational Flexibility: An unexpected change in operations may require manufacturers to reprogram AGVs to meet new demands.
- Dust-sensitive Sensors: AGVs rely heavily on sensors to navigate the warehouse floor. Dust and dirt particles can hamper the sensor’s ability to accurately calculate an AGV's location. Manufacturers must regularly clean the sensors and maintain a dust-free environment throughout the warehouse.
- Warehouse Space: While AGVs are more efficient than conveyors, they still require space and cannot move through highly narrow aisles. Manufacturers must consider their warehouse design and see where to implement AGVs for maximum benefit.
How Computer Vision Can Enhance AGVs?
Modern computer vision (CV) algorithms can significantly enhance AGVs’ navigation abilities by integrating them with state-of-the-art object detection and image segmentation models.
The following list highlights a few ways CV can optimize AGV operations.
- Flexible Navigation: CV can allow AGVs to dynamically create environment maps, detect objects, and segment the items to lift from the environment, store, and transport to distribution centers.
- More Precision: CV algorithms can accurately detect multiple objects simultaneously, allowing AGVs to move through the warehouse more precisely.
- Better Safety: An AGV with an integrated CV framework can recognize harmful objects and avoid paths that may cause damage to its parts with segmentation.
- Defect Detection: CV-based AGVs can detect anomalies in raw materials, work-in-process, and finished goods and send immediate notifications to the relevant teams for instant resolution.
- Data-driven Decisions: Manufacturers can connect CV-based AGVs with their warehouse management systems (WMS) to get relevant real time floor data. They can extract actionable insights from this data to improve warehouse design and optimize AGV movements.
Data Platform for High-Performing AGV Models
Using Encord’s data development platform, you can annotate and curate high-quality visual datasets to train your AGV systems to detect and navigate their environment better. Encord allows you to:
- Precisely annotate the visual datasets containing objects and scenes the AGV will operate in (with Annotate).
- Automatically find dataset quality issues you can quickly flag and fix (with Index).
- Use data-centric evaluations to test the generalizability of your CV model before deploying it on the AGV (with Active).
Analyzing and Annotating Industrial Robot datasets in Encord.
Automated Guided Vehicles (AGVs): Key Takeaways
AGVs are becoming necessary for modern manufacturing plants to boost efficiency and profitability. With businesses rushing to automate their operations using AI and robotics, AGVs are the cornerstone of today’s strategic initiatives to beat the competition.
Below are a few key points you should remember regarding AGVs.
- AGV Types: AGVs come in multiple shapes and forms. The most common AGV types include AGCs, Forklift AGVs, Unit-load AGVs, Towing AGVs, Heavy Burden Carriers, Hybrid AGVs, and Automated Mobile Robots (AMRs).
- AGV Operation: AGVs consist of a navigation system, a steering mechanism, a traffic control system, and a battery charging method.
- AGV Applications: AGV use cases include transporting raw materials, finished goods, and work-in-process. They also help with pallet, trailer, and roll handling.
Explore our products
- The main components of AGVs include a navigation system, steering mechanism, power system, and traffic control system.
- Best practices include regular maintenance, software updates, staff training to handle machinery efficiently, and optimizing warehouse design for clear navigation.
- Autonomous vehicles can help reduce costs by minimizing labor costs, preventing downtime, increasing accuracy, optimizing storage, and protecting goods from damage.
- The future of AGVs includes artificial intelligence for building sophisticated navigation systems, integration with Internet-of-Things (IoT), and data analytics solutions.
- Machine vision enhances AGVs by allowing them to flexibly navigate complex objects, detect obstacles, and recognize relevant objects to pick, store, and deliver to the desired distribution and production sites.