Contents
Role of Computer Vision in Warehouse Automation
Key Applications of Computer Vision in Warehouse Automation
Computer Vision Implementation Strategies in Warehouse Automation
Benefits of Computer Vision in Warehouse Automation
Challenges of Using Computer Vision in Warehouse Automation
Conclusion
Encord Blog
How to Leverage Computer Vision in Warehouse Automation
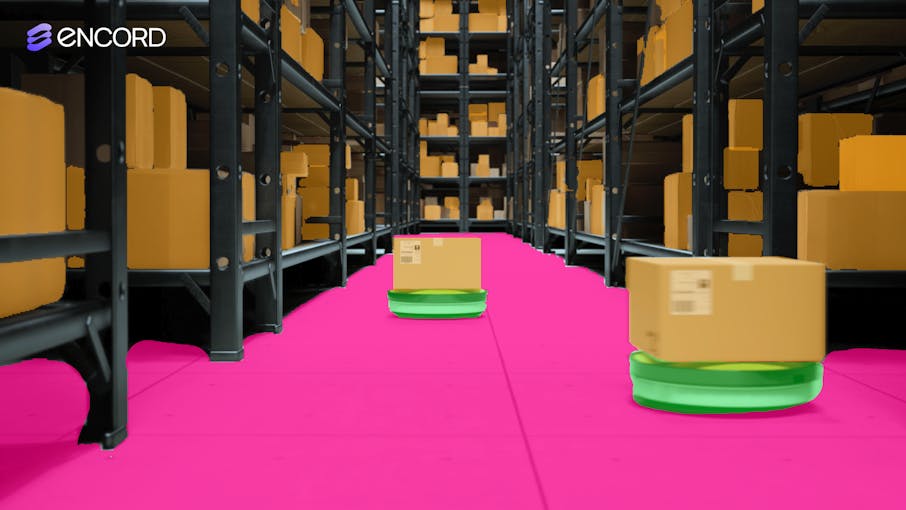
In today's fast-paced supply chain environment, warehouses must operate efficiently and accurately to keep up.
Manual processes often cause errors, inefficiencies, and safety risks, making it hard for warehouses to meet modern logistics demands.
A key challenge is keeping accurate inventory levels and ensuring the proper handling and shipment of goods.
Warehouse automation addresses these challenges by using technology to perform tasks and processes with minimal human intervention.
This includes deploying robotics, automated storage and retrieval systems (AS/RS), automated guided vehicles (AGVs), conveyor systems, and software solutions like warehouse management systems (WMS).
The goal is to streamline operations, enhance efficiency, reduce errors, and improve overall productivity.
Computer vision (CV) plays a pivotal role in revolutionizing warehouse automation. It enables machines to interpret and understand visual data using cameras, automating tasks traditionally performed by human workers.
In this article, you will learn about the impact of CV on warehouse automation. You will explore key applications using CV in warehouse automation.
After reading this article, you will understand how CV improves warehouse efficiency, accuracy, and safety and how to use it to optimize logistics processes.
Role of Computer Vision in Warehouse Automation
Computer vision (CV) is essential to improving warehouse automation by enabling systems to interpret and act on visual data.
It transforms warehouse operations, from inventory management to quality control, significantly improving efficiency, accuracy, and safety.
Computer Vision powered Robotic Arm (Source)
Here’s a detailed look at the role of computer vision in warehouse automation:
Automated Data Capture
CV systems continuously capture visual data from the warehouse environment, converting it into actionable insights. This automated data capture reduces the need for manual data entry and ensures real-time updates.
Object Detection and Tracking
CV algorithms detect and track objects, such as products, pallets, and equipment, within the warehouse. This capability is essential for maintaining accurate inventory records, monitoring the movement of goods, and optimizing storage layouts.
Quality Assurance
By analyzing visual data, CV systems can identify defects, damages, or non-compliance with quality standards. This role is crucial for maintaining high product quality and minimizing errors.
Spatial Awareness and Navigation
CV provides spatial awareness to robotic systems, enabling them to navigate the warehouse environment safely and efficiently. This includes avoiding obstacles, finding optimal paths, and coordinating movements with other robots or humans.
Environmental Monitoring
Vision systems monitor environmental conditions such as lighting, temperature, and humidity. This role ensures that products are stored under optimal conditions and helps in maintaining the integrity of sensitive goods.
Security and Safety
CV enhances warehouse security by monitoring for unauthorized access, theft, or other security breaches. Additionally, it plays a vital role in ensuring workplace safety by detecting hazardous conditions and ensuring compliance with safety protocols.
Key Applications of Computer Vision in Warehouse Automation
In this section, you will learn key examples of CV applications in warehouse automation. These real-world examples illustrate how computer vision revolutionizes warehouse operations, enhancing efficiency, accuracy, and safety in warehouse processes.
Automated Inventory Management
Automated inventory management using computer vision involves cameras, sensors, and CV algorithms and models (such as YOLO, SSD, R-CNN, etc.) to monitor and manage inventory levels in real-time.
This enables the automated identification, tracking, and counting of items, automatically updating inventory records, and triggering reordering processes when stock levels are low within a warehouse.
High-resolution cameras and sensors are strategically placed throughout the warehouse. These devices continuously capture images and video of the inventory, shelves, and storage areas.
Automated inventory system KoiVision (Source: NVIDIA Blogs)
The captured visual data is processed using CV algorithms. These algorithms can detect and recognize items, read barcodes or QR codes, and assess the quantity and condition of the inventory.
The systems provide real-time updates on inventory levels. The system automatically adjusts the inventory records to reflect these changes as items are added or removed.
The CV system is integrated with the warehouse management system, enabling real-time synchronization of inventory data.
For example, PepsiCo uses computer vision technologies from KoiReader to inspect labels for efficient inventory management and distribution operations.
Order Picking and Packing
Order picking and packing using CV uses object detection and recognition to automate and optimize the selection and packaging of items for shipment in a warehouse.
Robotic systems equipped with CV identify, pick, and pack items for shipment. Vision systems ensure the correct items are picked and packed, minimizing errors.
Cameras and sensors are installed throughout the picking and packing areas or on robotic arms. These devices continuously capture images and video of items, shelves, and packaging stations.
Computer vision algorithms analyze the visual data to identify items by recognizing shapes, sizes, barcodes, QR codes, and other visual markers. The system determines the exact location of each item. In the packing area, computer vision systems assist in selecting the appropriate packaging materials and methods for each item.
For example, Ocado, the UK-based online supermarket, uses robotic arms guided by computer vision to pick up groceries. The vision systems help the robots identify products, pick them up without damaging them, and efficiently place them into customer orders.
Ocado robotic arms guided by Computer Vision (Source: BBC)
Autonomous Mobile Robots (AMRs)
AMRs are robots capable of navigating complex and dynamic environments without physical guidance.
They use sophisticated sensors and algorithms to understand and interpret their surroundings. AMRs use computer vision, LiDAR, and other sensors to create and continuously update maps of their environment to navigate the warehouse environment, transport goods, and avoid obstacles.
Vision systems provide real-time feedback for route optimization and collision avoidance, enabling AMRs to dynamically plan and adjust their paths based on real-time environmental data. Computer vision allows AMRs to recognize objects, thus helping them interact with them, such as picking items from shelves or placing them in designated areas.
Fetch Robotics deploys AMRs equipped with computer vision for warehouse material handling tasks. These robots can navigate complex environments, transport goods between locations, and work alongside human workers.
Fetch Robotics’ Freight1500 has zero blind spots and 360° robot vision. (Source: Fetch Robotics.)
Sorting and Categorizing
Sorting robots are stationary (e.g., XYZ Gantry Robots, Robotic Arms) and mobile variants designed to swiftly and effectively organize goods and parcels based on their destination and categorization criteria.
These robots use sensors, cameras, actuators, and mechanical components to detect, identify, and classify objects accurately before sorting them into designated locations. This automated process enhances logistics and distribution operations efficiency, ensuring precise handling and timely delivery of items to their intended destinations.
For example, Unbox Robotics’ Elevated Mobile Robots (EMRs) are specifically engineered for automated material handling and sorting tasks within warehouses and distribution centers. See this article to learn more.
These robots often have elevated platforms or track systems, enabling them to navigate above and around warehouse machinery and obstacles. Using different sensors and CVs, EMRs can accurately identify and categorize items based on various attributes, such as size, shape, weight, and other distinguishing features.
This capability allows them to efficiently manage sorting tasks, contributing to streamlined warehouse operations and enhanced logistical efficiency.
Unbox Robotics’ AMRs for sorting (Source: Unbox Robotics)
Safety and Security Monitoring
Computer vision is critical to enhancing safety and security by continuously monitoring the environment, detecting potential hazards, and preventing unauthorized access. These systems analyze the visual data to detect potential safety hazards. This includes identifying spills, obstacles, unsafe stacking of goods, and malfunctioning equipment.
When a hazard is detected, the system can immediately alert warehouse personnel to address the issue. Using computer vision, worker behavior can be monitored to ensure compliance with safety protocols.
For example, it can detect whether employees wear required personal protective equipment (PPE), such as helmets, gloves, and safety vests. It can also monitor for unsafe behaviors, such as workers entering restricted areas or operating machinery improperly.
CV can be integrated with access control systems to prevent unauthorized entry. By using facial recognition and other biometric data, the system ensures that only authorized personnel can access sensitive areas.
For example, Protex AI, a CV startup, collaborated with DHL on a proof-of-concept project utilizing their AI-based unsafe event capture solution.
Workplace safety monitoring at DHL warehouse (Source: DHL)
Palletizing and Depalletizing
Palletizing and depalletizing are critical processes in warehouse operations. Palletizing involves arranging products onto a pallet for storage or transportation, while depalletizing involves removing products. Using CV in these processes enhances efficiency, accuracy, and safety.
In this process, cameras and sensors capture images of products, determining their size, shape, orientation, and position. This data is crucial for creating an optimal arrangement on the pallet.
The visual data is then analyzed to identify and classify the items. This step ensures the system understands what items must be palletized and how they should be arranged. The system calculates how to arrange items on a pallet to maximize space and stability. This involves determining the most efficient stacking pattern and orientation for each item.
For example, Mech-Mind’s AI+3D industrial robot solution uses computer vision in warehouses to palletize and depalletize cartons. The 3D vision system, which uses Mech-Eye DEEP 3D vision camera, generates precise point cloud data while AI algorithms position suction cups correctly for accurate grabbing.
Quickly recognizing new cartons and handling various random pallet patterns optimize consistency and efficiency.
Palletizing and depalletizing cartons in Warehouse (Source: Mech-Mind)
Label Verification
Label verification is critical in warehouse operations to ensure that products are correctly identified, tracked, and processed. CV enhances the accuracy and efficiency of label verification by automating the reading and verification of product labels.
CV algorithms analyze the images on products to read text, barcodes, QR codes, and other label information. This enables the system to extract crucial details such as product codes, descriptions, batch numbers, and expiration dates.
The extracted label information is compared against data in the warehouse management system (WMS). The system verifies that the labels match the expected data for each product, ensuring accuracy in identification and inventory management.
Label verification for quality control (Source: OpenCV AI)
Computer Vision Implementation Strategies in Warehouse Automation
Implementing computer vision in warehouse automation involves careful planning and execution to ensure successful integration and maximized benefits.
Image Source: baslerweb.com
Here are key implementation strategies:
Needs Assessment and Goal Setting
Conduct a thorough assessment of the warehouse operations to identify specific areas where computer vision can add value. Define clear objectives such as improving accuracy, reducing labor costs, enhancing safety, or increasing operational efficiency. Following are the action steps that must be taken:
- Engage stakeholders to understand pain points.
- Map out current processes and identify bottlenecks.
- Set measurable goals for the computer vision implementation.
Choosing the Right Technology and Vendors
Select appropriate computer vision technologies and tools that align with your objectives. Consider factors such as accuracy, speed, scalability, and ease of integration. Following are the action steps that must be taken:
- Evaluate different computer vision algorithms (e.g., CNNs, YOLO, SSD).
- Consider hardware requirements, including cameras, sensors, and computational resources.
- Choose software platforms and libraries (e.g., OpenCV, TensorFlow, and PyTorch) that support your needs.
Develop and Train Models
Create and train models customized to your warehouse's specific tasks, such as object detection, classification, or segmentation. Following are the action steps that must be taken:
- Collect and annotate a diverse set of training data representative of the warehouse environment.
- Train models using supervised learning techniques and validate their performance on test datasets.
- Optimize models for accuracy and efficiency, using transfer learning to leverage pre-trained models.
Integrate with Existing Systems
Ensure seamless integration of computer vision systems with existing warehouse management systems (WMS), enterprise resource planning (ERP) systems, and other relevant software. Incorporate EDI ERP integration to streamline communication and data exchange between computer vision systems, WMS, and ERP software, ultimately enhancing operational efficiency.
The following are the action steps that must be taken:
- Use APIs and middleware to connect computer vision systems with WMS and ERP systems.
- Ensure data compatibility and synchronization between systems.
- Develop custom integration solutions if necessary.
Maintenance and Continuous Improvement
Implement a maintenance plan to ensure the computer vision systems remain operational and effective. To put in place a robust maintenance plan, you must consider the following action steps:
- Establish regular maintenance schedules for hardware components such as cameras and sensors.
- Monitor system performance and conduct periodic reviews to identify areas for improvement.
- Update software and models to incorporate new features or address emerging challenges.
- Continuously improve the system based on performance data and feedback.
How Encord Helps with the Continuous Improvement of Warehouse Automation Systems
You can improve your warehouse automation and maintenance strategies with a platform like Encord, which offers three products:
- Encord Annotate to help label the visual datasets you collect from the warehouse and sites through vision-based sensors,
- Encord Index to help curate and manage the scale of the visual dataset,
- If you train computer vision models at scale, Encord Active can help you test and evaluate the model's performance before you deploy it to the system.
Benefits of Computer Vision in Warehouse Automation
Implementing computer vision (CV) in warehouse automation brings numerous advantages that significantly enhance operational efficiency, accuracy, and safety.
Warehouse automation using robots and AMRs (Source: roboticstomorrow.com)
The following are some key benefits:
Increased Efficiency
CV automates tasks such as inventory management, sorting, and quality control, which speeds up processes that would otherwise be time-consuming if done manually. It results in:
- Faster order processing and fulfillment.
- Reduced cycle times for inventory counting and verification.
- Improved throughput in sorting and packing operations.
Enhanced Accuracy
CV systems provide precise and consistent analysis of visual data, reducing human error in tasks such as counting, sorting, and inspecting goods, resulting in:
- More accurate inventory records and reduced stock discrepancies.
- Fewer picking and packing errors, leading to improved customer satisfaction.
- Precise defect detection and quality control, ensuring higher product quality.
Improved Safety
Computer vision systems can continuously monitor the warehouse environment for potential safety hazards, such as obstacles, spills, or unsafe behavior, and alert staff to take preventive measures, resulting in:
- Reduced risk of accidents and injuries.
- Enhanced compliance with safety regulations.
- Real-time alerts and interventions to prevent hazardous situations.
Enhanced Quality Control
CV systems can inspect products for defects, damages, or non-compliance with quality standards, ensuring that only high-quality products are shipped to customers. It results in:
- Improved product quality and consistency.
- Reduction in returns and customer complaints.
- Increased customer satisfaction and brand reputation.
Challenges of Using Computer Vision in Warehouse Automation
Image Source: DHL
- High Initial Investment: Implementing computer vision systems can be costly due to the need for high-quality cameras, computing resources, and networking infrastructure.
- Integration with Existing Systems: Integrating new computer vision technologies with existing warehouse management systems (WMS) and processes can be complex and time-consuming.
- Data Privacy and Security Concerns: Capturing and storing visual data can raise privacy issues and expose the system to cybersecurity threats.
- Accuracy and Reliability of Vision Systems: Computer vision systems can sometimes struggle with accuracy due to varying lighting conditions, occlusions, or environmental changes.
- Complexity of Implementation: Setting up and configuring computer vision systems requires technical expertise and can be complex.
- Scalability Issues: As the volume of data increases, the system needs to scale accordingly, which can be challenging.
- Technical Limitations: Computer vision technology is still evolving, and there may be limitations in the algorithms' ability to recognize and interpret certain objects or scenarios.
Conclusion
We can reduce manual labor and associated errors by automating various tasks, such as inventory management, sorting, quality control, and safety monitoring, leading to faster and more reliable warehouse operations.
Implementing computer vision involves strategic planning, including assessing needs, selecting appropriate technologies, training machine learning models, integrating systems, and conducting pilot tests. These steps ensure that the systems are scalable, flexible, and capable of adapting to dynamic warehouse environments.
Key benefits of computer vision in warehouse automation include increased efficiency, improved accuracy, enhanced safety, real-time data and insights, cost savings, scalability, quality control, predictive maintenance, and improved security.
These advantages collectively contribute to a more streamlined and effective warehouse operation, supporting businesses in meeting customer demands and maintaining a competitive edge.
Planners must carefully plan, implement robust security measures, and continuously maintain the system to address challenges such as high initial setup costs, integration complexities, and data privacy concerns.
The future of computer vision in warehouses looks promising, with advancements in AI algorithms, IoT integration, and more efficient hardware solutions expected to further enhance its capabilities.
Explore our products
- Computer vision in warehouse automation refers to the use of cameras, sensors, and advanced algorithms to enable machines to interpret and understand visual data. This technology is used to automate various tasks such as inventory management, sorting, quality control, and safety monitoring in warehouses.
- Computer vision improves efficiency by automating repetitive and time-consuming tasks, such as inventory counting, item sorting, and defect detection. This reduces the need for manual labor, speeds up processes, and minimizes errors, leading to faster order fulfillment and improved operational throughput.
- Key applications include, Automated inventory management and cycle counting, Object detection and sorting, Quality control and defect detection, Safety monitoring and hazard detection, Automated guided vehicles (AGVs) and robotics navigation.
- Challenges include, High initial setup costs, Integrating computer vision with existing warehouse management systems, Ensuring data privacy and security, Managing the complexity of the technology and maintaining it, Handling diverse and dynamic warehouse environments.
- The hardware required includes high-resolution cameras, 3D sensors, LiDAR systems, computational resources such as GPUs for processing visual data, and sometimes specialized lighting to ensure optimal image capture conditions.
- Yes, modern computer vision systems are designed to work in various lighting conditions. They can utilize infrared sensors, thermal cameras, or adaptive algorithms that adjust to different lighting environments to ensure reliable performance.
- Computer vision systems are trained using machine learning algorithms on diverse datasets that include various product types and packaging. This allows them to recognize and process different items accurately, regardless of their size, shape, or packaging.
- Integration is achieved through APIs and middleware that connect the computer vision system with the WMS. This allows for seamless data exchange and synchronization, enabling real-time updates and cohesive operation across different systems within the warehouse.
- Yes, data privacy is a significant concern. Warehouses must ensure that visual data is securely stored and processed, with access controls and encryption in place. Compliance with data protection regulations, is also essential to protect employee and business data.
- Future advancements may include more sophisticated AI algorithms for better object recognition, improved integration with IoT devices, enhanced real-time analytics capabilities, and more affordable and efficient hardware solutions, making the technology more accessible and effective.