Contents
What is Smart Robotics?
Core Components of Smart Robotics
The Six Most Common Types of Smart Robots
Why Smart Robots Are Gaining Popularity
Consumer and Commercial Applications of Smart Robotics
Best Practices for Building Smart Robotics
What are the Challenges with Smart Robots Today?
How Encord Helps Build Smart Robotics
Smart Robots: Key Takeaways
Encord Blog
Smart Robotics: Definition & How it Works
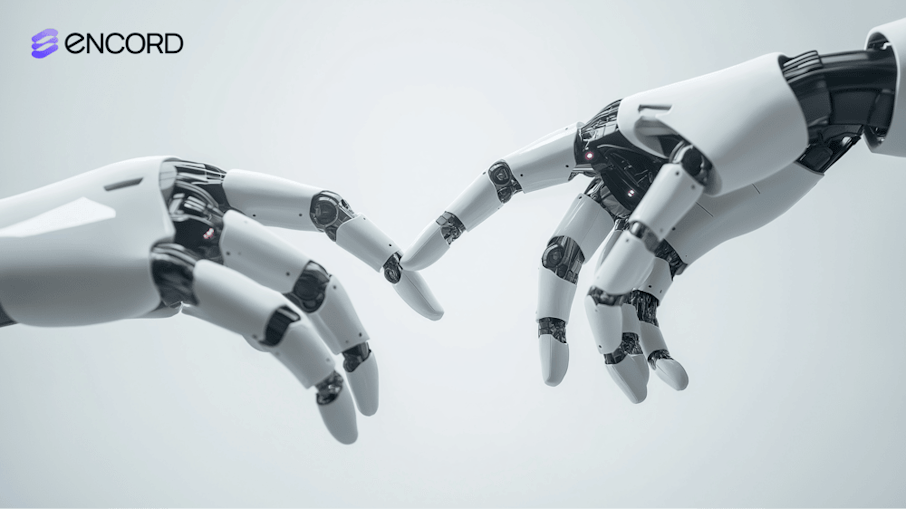
The global smart robot market is experiencing rapid growth, with projections estimating it will reach approximately $834 billion by 2037. This growth is driven by advancements in artificial intelligence (AI), deep learning, and sensor technologies that enable autonomous robots to perform complex tasks across various industries.
Traditional robots operate based on pre-programmed instructions and perform specific tasks. However, smart robots can perceive their environment, learn from their experiences, and autonomously adapt to new situations.
Moreover, smart robots contribute to substantial cost savings. For instance, the U.S. Air Force has implemented robotic solutions that have saved approximately $8.8 million since 2016, equating to $220,000 per aircraft in maintenance costs.
Despite their transformative potential, developing smart robots poses significant challenges, from managing massive datasets and fine-tuning advanced algorithms to addressing the complexities of real-world environments.
In this post, we will discuss what smart robotics are, their use cases, benefits, and challenges. We will also go over how platforms like Encord can help overcome data issues and help experts build more efficient autonomous robotic systems.
What is Smart Robotics?
Smart robots are autonomous machines designed to perform complex physical tasks using advanced robotics technologies, AI, and ML. They adapt to changing environments and work alongside humans to assist them in several domains.
For example, Amazon uses mobile robots called Proteus, which work collaboratively with human staff. These robots can coordinate directional changes and assist humans with navigation using advanced vision. The technique improves operational efficiency while maintaining safety and streamlining workflows in dynamic environments.
Proteus, Amazon’s autonomous mobile robot
Core Components of Smart Robotics
Smart robots use several components to process information and act appropriately. Below, we will discuss the key components of smart robotics.
Sensors and Perception
Smart robots interpret their surroundings using different sensors. Visual sensors, such as cameras and LiDAR systems, provide detailed spatial data, while auditory and tactile sensors help them understand the environment in different dimensions.
Sensors collect important data such as distance, texture, temperature, and movement from different sources. Fusing this data allows the robot to create a comprehensive model of its environment, enabling accurate navigation and informed decision-making in real time.
Processing Units and Artificial Intelligence
Processing units in smart robots act as a "brain," often including Central Processing Units (CPUs), Graphics Processing Units (GPUs), and specialized AI accelerators. These units are integrated with advanced AI algorithms to handle the massive influx of sensory data in real time.
Processing units run ML algorithms, particularly neural networks, to enhance robot intelligence.
For instance, robots on the factory floor use AI to plan efficient routes and refine their paths by learning from past trips. This cognitive capability distinguishes smart robots from traditional machines with fixed programming.
Actuators and Movement Mechanisms
After the robot perceives its environment and processes the necessary data, actuators help convert the information into physical action. These actuators act like motors or hydraulic systems to execute movements and interactions.
The robot's ability to perform tasks depends on the seamless coordination between perception and action. The processing unit, guided by sensor data and AI, directs the actuators to execute specific movements, enabling the robot to navigate, manipulate objects, and carry out its intended tasks within its environment.
The Six Most Common Types of Smart Robots
Robots come in various forms, each designed for specific tasks and environments. Here are six common types of robots:
Autonomous Mobile Robots (AMRs)
AMRs operate independently and can navigate their environment intelligently without needing physical guides or pre-programmed paths. They use sensors and onboard processing to perceive their surroundings, map environments, and make decisions about navigation and task execution.
AMRs are flexible, adaptable, and ideal for dynamic environments like warehouses, hospitals, and public spaces.
Automated Guided Vehicles (AGVs)
AGVs are material-handling robots that follow predefined paths using wires, magnetic strips, or lasers. Unlike AMRs, AGVs are less flexible as they follow fixed routes and need changes to the setup, like moving strips or wires, to adjust their paths. However, they are suitable for repetitive tasks like moving parts along a factory assembly line or carrying boxes to a shipping area.
Articulated Robots
Articulated robots are robotic arms with rotary joints (similar to those of a human arm) that allow for a wide range of motion and flexibility. They usually have two to ten joints or more.
Articulated robots are used for various applications, such as assembly, welding, painting, and material handling in manufacturing and industrial settings. Their dexterity and reach make them suitable for complex and precise tasks, like assembling tiny phone parts or welding car frames.
Articulated robots - robotic arms
Humanoids Robots
Mobile humanoid robots can mimic human form and behavior for tasks that require human-like interactions. They are developed for research, education, and public relations, focusing on exploring human-robot interaction. For instance, Pepper from SoftBank Robotics welcomes guests and promotes products at events, serving as a friendly face for public relations.
Although still under development for broad practical use, organizations are considering them for use in customer service, elder care, and potentially dangerous environments.
For example, Stanford’s OceanOneK, a humanoid diving robot, explores deep-sea shipwrecks at depths reaching 1,000 meters, where conditions are too hazardous for human divers.
Collaborative Robots (Cobots)
Cobots work safely alongside humans in a shared workspace. They are equipped with sensors and safety features to detect human presence and avoid causing injury.
Compared to traditional industrial robots, collaborative robots are smaller, can be used more flexibly, and are easier to program. They assist humans across various tasks, boosting productivity and safety in manufacturing, assembly, and certain service applications.
Hybrid Robots
Hybrid robots combine various capabilities of different robot types, such as wheeled mobile robots, aerial drones, or robotic arms. Their flexibility allows them to handle tough jobs that need multiple skills like flying high to check crops or gripping tools to fix underwater pipes. These autonomous systems are ideal for complex workflows that require versatility and precision.
Why Smart Robots Are Gaining Popularity
Smart robots are experiencing increased adoption across various industries due to their potential to enhance productivity, efficiency, and safety. Several factors contribute to their growing popularity:
- Improved Productivity: Smart robots automate repetitive tasks, freeing human workers for more complex responsibilities. They boost productivity for large manufacturers by enabling continuous operations without extra labor costs.
- Enhanced Efficiency: Smart robots streamline warehouse operations by automating inventory management and order fulfillment, significantly reducing operational costs. For instance, Amazon warehouses featuring robots like Proteus have achieved up to a 25% reduction in operational costs and savings of up to $10B/year.
- Increased Safety: Smart robots can handle hazardous tasks, reducing the risk of accidents and injuries. In industries like construction, robots assist in tasks such as bricklaying, welding, and demolition, increasing efficiency and safety on-site.
- Predictive Maintenance: Smart robots use advanced sensors and ML algorithms to detect and analyze data from equipment, identifying potential issues before breakdowns occur. This enables the scheduling of maintenance activities in advance, reducing downtime and extending machinery life.
- Enhanced Product Quality: Smart robots can detect flaws during manufacturing with integrated sensors and data analysis capabilities This reduces the number of defective products reaching the market. They can also monitor production processes in real-time, adjusting settings to improve quality.
- Reduced Overhead Costs: Smart robots can deliver quick returns on investment by automating specific job roles and lowering health and safety costs. They also require less space and can work alongside humans, allowing businesses to downsize to more cost-effective workplaces.
Consumer and Commercial Applications of Smart Robotics
Households and workplaces are quickly adopting smart robots to simplify tasks and enhance productivity. Below are key areas where their versatility makes them valuable in both consumer and commercial settings.
Consumer Applications
Smart robots are becoming more integrated into our homes, improving convenience, companionship, and assistance in daily life.
Smart Home Assistants
Robotic vacuums like the Roomba iRobot use AI and sensors to autonomously navigate homes, clean floors, and adapt to changing layouts. These robots learn user habits over time and optimize cleaning schedules and routes for maximum efficiency.
Companion Robots
Beyond chores, robots like Pepper or ElliQ interact with humans, provide companionship, and assist the elderly. They can monitor daily routines, remind users to take medications, and provide entertainment, enhancing the quality of life for vulnerable populations.
Commercial Applications
In the commercial sector, smart robots streamline operations, reduce costs, and enable businesses to scale efficiently.
Manufacturing
Collaborative robots (cobots) such as ABB’s YuMi or UR5e solder work alongside humans on production lines. In electronic manufacturing, cobots solder tiny components with unmatched accuracy, cutting errors and speeding up output. They handle repetitive or hazardous tasks, letting workers focus on higher-value roles.
Warehouse Automation
Autonomous mobile robots (AMRs) from companies like Fetch Robotics (acquired by Zebra Technologies) and Locus Robotics maintain high throughput in large-scale e-commerce and logistics operations. These robots zip around warehouses, retrieving items, delivering them to pickers, and restocking shelves, all without human guidance.
Locus Robotics fulfillment archives
Healthcare
Surgical robots like da Vinci bring AI-enhanced precision to operating rooms. Surgeons use robotic arms to perform minimally invasive procedures, like heart surgeries, with smaller incisions, leading to faster recoveries. Meanwhile, disinfection robots welding UV light sanitizer hospital spaces, reducing infection risks without harming staff.
Security
AI-powered surveillance robots provide proactive and responsive solutions in the security and surveillance domain. Security robots like SAM3 can monitor environments continuously without constant human intervention, which is valuable in critical security environments. They can also react instantly to suspicious events, alerting human operators.
Autonomous security robot SAM3
Best Practices for Building Smart Robotics
Developing and implementing smart robotic solutions requires careful planning and execution. These best practices can help you maximize the benefits of smart robotics while minimizing potential challenges.
- Define Clear Objectives: Before you start building a smart robot, be clear about what it needs to do. What problems are you trying to solve? What specific tasks will the robot perform? Clearly defining the goals for implementation is the first and most important step.
- Choose the Right Technology: Select appropriate sensors, processors, actuators, and AI algorithms based on the application's specific requirements. When choosing hardware and software components, consider factors such as accuracy, reliability, and compatibility.
- Focus on Integration and Interoperability: Ensure seamless integration between different components of the robotic system and with existing IT infrastructure. Try to use open standards and protocols to promote interoperability and avoid vendor lock-in.
- Prioritize Safety and Security: Implement powerful safety measures to protect humans working alongside robots, including safety barriers, photoelectric barriers, and scanners in monitored zones. Incorporating security measures can help you to protect your robot from data theft and unauthorized access.
- Focus on Learning and Adaptation: Smart robots get smarter over time by learning. Machine learning techniques enable robots to learn from experience and adapt to changing environments. Data fusion combines data from different sensors to form a comprehensive understanding of the surroundings.
- Promote Human-Robot Collaboration: Robots work as helpers, so design them in a way that they can work alongside humans, augmenting their capabilities and improving productivity. Provide training and support to human workers to ensure effective collaboration with robots.
- Use Simulation and Testing: Before deploying your robot physically, employ simulation tools to test and refine its capabilities in a virtual environment. Use iterative testing cycles to allow for quick adjustments and improvements.
- Monitor Performance and Optimize: Continuously monitor smart robot performance and identify areas for improvement. Use data analytics to optimize robot behavior and enhance overall system efficiency.
What are the Challenges with Smart Robots Today?
Despite the advancements and potential benefits of smart robots, several challenges make their broad adoption and optimal performance difficult. Data challenges stand out as one of the most critical barriers to achieving the full potential of smart robotics.
- Data Quality and Quantity: Smart robots require large amounts of high-quality data to learn effectively. Insufficient or inaccurate data can impede their learning and performance. Acquiring enough representative data to reflect real-world situations can be both difficult and expensive.
- Data Annotation and Labeling Complexity: ML models within intelligent robots rely on accurately labeled data. The annotation process is labor-intensive, time-consuming, and prone to human error, which can slow down the development and refinement of robotic capabilities.
- Real-Time Data Processing: Smart robots must understand the world as it happens, not later. They constantly get data from sensors and process it quickly to make decisions in real time. Processing all this sensor data requires powerful computers and scalable software that can handle large data volumes.
- Data Security and Privacy Concerns: Smart robots collect large amounts of data about their environments, some of which may be sensitive. Ensuring the security and privacy of this data requires robust measures and clear protocols, adding complexity and cost to robot development.
- High Development and Operational Costs: The initial investment in smart robotics, including research and development, hardware, and system integration, can be substantial. Ongoing expenses related to maintenance, upgrades, and continuous AI model training further affect affordability.
How Encord Helps Build Smart Robotics
As discussed above, building efficient smart robots presents numerous challenges, primarily due to the inherent data complexities. Smart robotics relies heavily on high-quality data to train AI models, and issues like noisy sensor inputs, inconsistent annotations, and real-time processing can negatively impact performance. Advanced data management tools like Encord are necessary to address these data challenges.
Encord is a leading data development platform for AI teams that offers solutions to tackle issues in robotics development. It enables developers to create smarter, more capable robot vision models by streamlining data annotation, curation, and visualization. Below are some of its key features that you can use for smart robotics development.
Intelligent Data Curation for Enhanced Data Quality
Encord Index uses semi-supervised learning to assess data quality and detect anomalies, such as blurry images from robotic cameras or misaligned sensor readings. It can detect mislabeled objects or actions and rank labels by error probability. The approach reduces manual review time significantly.
Precision Annotation with AI-Assisted Labeling for Complex Robotic Scenarios
Human annotators often struggle to label the complex data required for smart robots. Encord addresses this through advanced annotation tools and AI-assisted features. It combines human precision with AI-assisted labeling to detect and classify objects 10 times faster.
- Custom Ontologies: Encord allows robotics teams to define custom ontologies to standardize labels specific to their robotic application. For example, defining specific classes for different types of obstacles and robotic arm poses.
- Built-in SAM 2 and GPT-4o Integration: Encord integrates state-of-the-art AI models to supercharge annotation workflows like SAM (Segment Anything Model) for fast auto-segmentation of objects and GPT-4o for generating descriptive metadata. These integrations enable rapid annotation of fields, objects, or complex scenarios with minimal manual effort.
- Multimodal Annotation Capabilities: Encord supports audio annotations for voice model used robots that interact with humans through voice. Encord’s audio annotation tools use foundational models like OpenAI’s Whisper and Google’s AudioLM to label speech commands, environmental sounds, and other auditory inputs. This is important for customer service robots and assistive devices requiring precise voice recognition.
Maintaining Security and Compliance for Robotics Data
Encord ensures data security and compliance with SOC2, HIPAA, and GDPR standards, which are essential for managing sensitive data in robotics applications. Security is critical when handling potentially sensitive information like patient medical images used in surgical robots or personal voice data collected by companion robots. Encord’s commitment to security ensures data protection throughout the AI development lifecycle.
Smart Robots: Key Takeaways
Smart robotics is transforming industries by improving productivity, efficiency, and safety. These AI-powered machines autonomously execute tasks, learn from their surroundings, and work alongside humans. Below are some key points to remember when building and using smart robotics.
- Best Use Cases for Smart Robotics: Smart robotics excels in dynamic and complex environments that require automation, adaptability, and efficiency. This includes streamlining manufacturing assembly lines, optimizing warehouse logistics and fulfillment, enhancing surgical precision in healthcare, providing proactive security and surveillance, and delivering intelligent assistance in smart homes and elder care.
- Challenges in Smart Robotics: AI requires a large amount of high-quality data for effective learning, but collecting and labeling this data is complex and time-consuming. Real-time data processing is essential for robots to respond quickly and accurately, yet achieving this remains a hurdle. Also, ensuring data security and privacy is critical to prevent risks. Overcoming these challenges is essential for building reliable, high-performing smart robotic systems.
- Encord for Smart Robotics: Encord’s specialized data development platform, featuring AI-assisted annotation tools and robust data curation features, enhances the quality of training data for smart robots. These tools streamline data pipelines, improve data quality and quantity, ensure cost-effectiveness, and maintain data security. They can help the development and deployment of smarter, more capable robotic systems.
Explore our products
- Smart robots use sensors to see and hear their surroundings, AI to think and learn, and motors to move. They collect info, figure out what to do, and act independently, like a warehouse robot finding the fastest path to deliver a box.
- Autonomous Mobile Robots (AMRs): Move freely without set paths. Articulated Robots: Robots with arm joints for tasks like welding. Cobots: Help humans by lifting heavy items or performing risky jobs safely. Humanoids: Look and act like humans.
- A robotic system is all the parts that make a robot work together: sensors to sense, a computer brain to think, and motors to move.
- Smart robots improve automation by working independently, learning from mistakes, and adapting to changes. They handle dull or dangerous jobs, like stocking shelves, faster and safer than old robots or people, saving time and money.
- Smart robots boost manufacturing by assembling or welding quickly and without errors. They work nonstop, spot flaws with sensors, and team up with humans, like cobots soldering tiny parts, cutting costs, and speeding up production.